In the ever-evolving landscape of technology and engineering, the role of an instrumentation engineer stands out as both critical and multifaceted. These professionals are the backbone of industries ranging from manufacturing to aerospace, ensuring that complex systems operate smoothly and efficiently. But what exactly does an instrumentation engineer do? This article delves into the essential functions and responsibilities of these specialists, shedding light on their pivotal role in designing, developing, and maintaining the instruments that measure and control various processes.
Instrumentation engineers are not just technicians; they are innovators who bridge the gap between engineering principles and practical applications. Their expertise is vital for optimizing performance, enhancing safety, and driving advancements in automation and control systems. As industries increasingly rely on precision and data-driven decision-making, the demand for skilled instrumentation engineers continues to grow.
In this article, you will discover the key skills and qualifications required to become an instrumentation engineer, the diverse sectors they work in, and the challenges they face in a rapidly changing technological environment. Whether you are considering a career in this field or simply curious about the intricacies of engineering, you will gain valuable insights into the world of instrumentation engineering and its significance in shaping the future of technology.
Historical Background
Evolution of Instrumentation Engineering
Instrumentation engineering is a specialized field that has evolved significantly over the years, driven by advancements in technology and the increasing complexity of industrial processes. The roots of instrumentation engineering can be traced back to the early days of the Industrial Revolution in the 18th century when the need for precise measurement and control of processes became apparent. As industries began to grow, so did the demand for instruments that could monitor and control various parameters such as temperature, pressure, flow, and level.
Initially, instrumentation was rudimentary, relying on simple mechanical devices. For instance, the mercury thermometer, invented in the 17th century, was one of the first instruments used for temperature measurement. As industries expanded, the limitations of these early instruments became evident, leading to the development of more sophisticated devices. The 19th century saw the introduction of steam engines and other complex machinery, which necessitated the need for more accurate and reliable measurement tools.
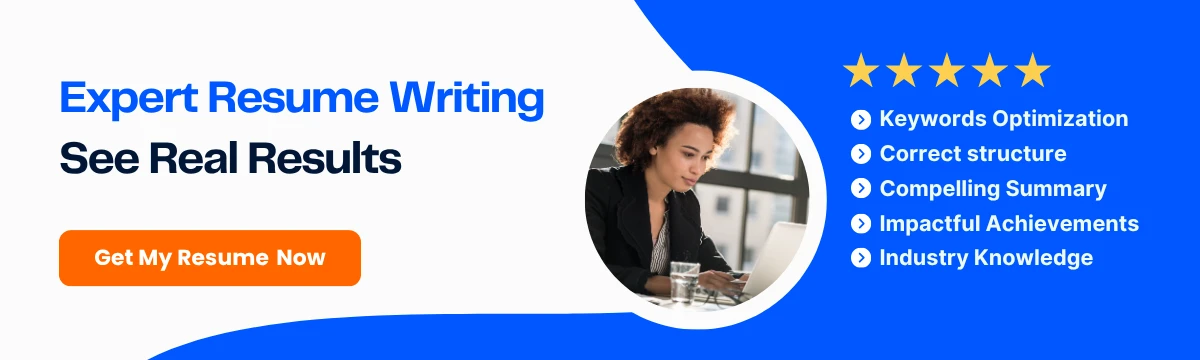
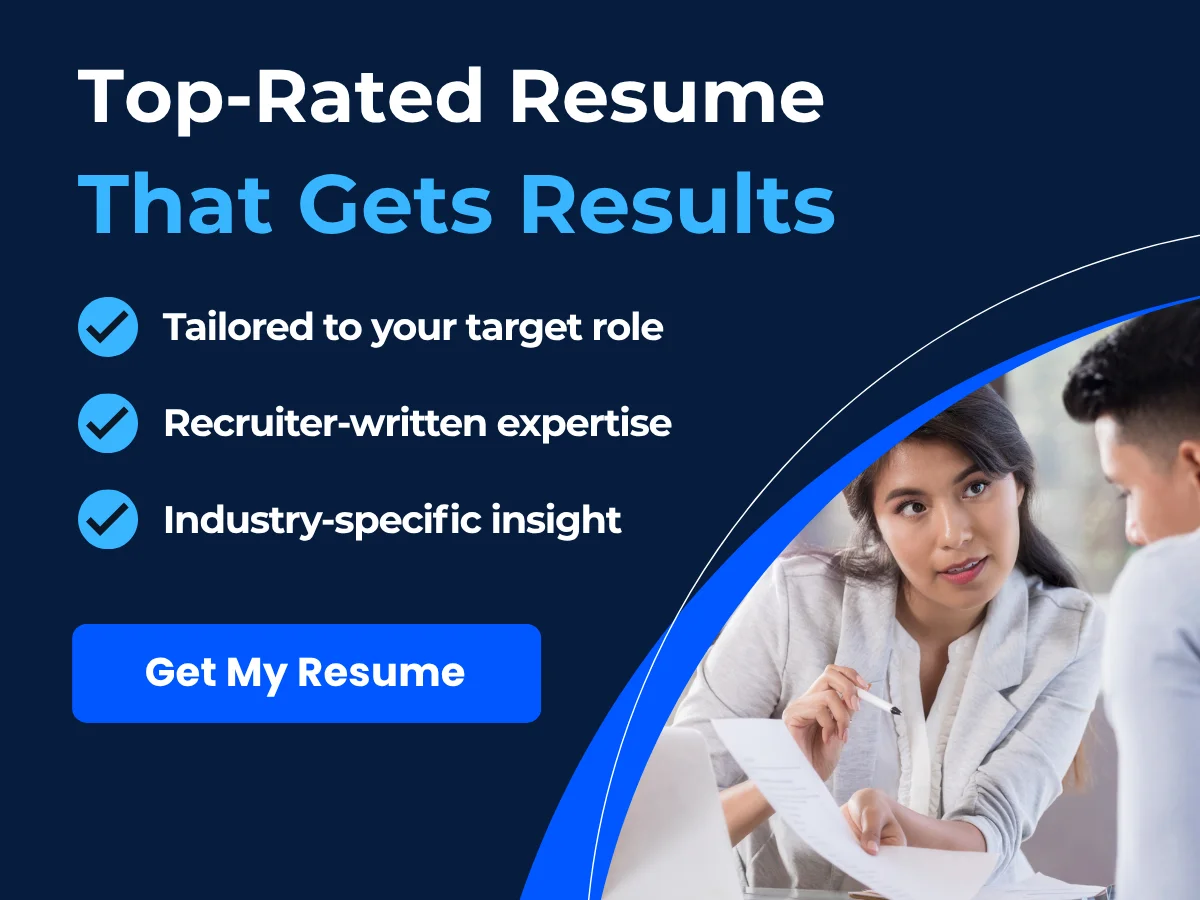
By the early 20th century, the field of instrumentation engineering began to take shape as a distinct discipline. The introduction of electrical and electronic components revolutionized the industry, allowing for the development of more advanced measuring instruments. The invention of the cathode ray oscilloscope in the 1930s, for example, provided engineers with a powerful tool for visualizing electrical signals, paving the way for further innovations in measurement technology.
Post-World War II, the rapid advancement of technology, particularly in electronics and computing, led to significant changes in instrumentation engineering. The advent of digital technology in the 1960s and 1970s marked a turning point, as analog devices began to be replaced by digital instruments that offered greater accuracy, reliability, and ease of use. This period also saw the emergence of automated control systems, which allowed for real-time monitoring and control of industrial processes, further enhancing efficiency and safety.
Key Milestones and Technological Advancements
Throughout its history, instrumentation engineering has been marked by several key milestones and technological advancements that have shaped the field as we know it today. Some of these milestones include:
- Development of Transducers: Transducers are devices that convert one form of energy into another, and their development has been crucial for instrumentation engineering. The invention of piezoelectric sensors in the mid-20th century allowed for the accurate measurement of pressure, force, and acceleration, leading to their widespread use in various industries.
- Introduction of Programmable Logic Controllers (PLCs): In the 1960s, PLCs emerged as a revolutionary technology in industrial automation. These digital computers are designed to control manufacturing processes and machinery, allowing for greater flexibility and efficiency in operations. PLCs have become a cornerstone of modern instrumentation engineering, enabling engineers to design complex control systems with ease.
- Advancements in Data Acquisition Systems: The development of data acquisition systems in the 1970s and 1980s allowed for the collection and analysis of data from various sensors and instruments. These systems have become essential for monitoring and controlling industrial processes, providing engineers with real-time insights into system performance.
- Rise of Wireless Technology: The late 20th and early 21st centuries saw the rise of wireless technology, which has transformed the way instrumentation systems are designed and implemented. Wireless sensors and communication protocols have enabled remote monitoring and control of processes, reducing the need for extensive wiring and improving system flexibility.
- Integration of IoT and Smart Technologies: The Internet of Things (IoT) has brought about a new era in instrumentation engineering. Smart sensors and devices can now communicate with each other and share data over the internet, allowing for enhanced monitoring, predictive maintenance, and improved decision-making. This integration of IoT technology has opened up new possibilities for automation and control in various industries.
These milestones represent just a few of the significant advancements that have shaped instrumentation engineering. As technology continues to evolve, the field is likely to see further innovations that will enhance the capabilities of instrumentation systems and improve their application across various sectors.
Instrumentation engineering today encompasses a wide range of applications, from process control in manufacturing to environmental monitoring and healthcare. The discipline has grown to include various subfields, such as control engineering, measurement science, and automation, reflecting the diverse nature of modern industrial processes.
The evolution of instrumentation engineering has been driven by the need for accurate measurement and control in increasingly complex industrial environments. Key milestones and technological advancements have played a crucial role in shaping the field, leading to the development of sophisticated instruments and systems that are essential for modern industry. As we look to the future, instrumentation engineering will continue to adapt and innovate, ensuring that it remains at the forefront of technological progress.
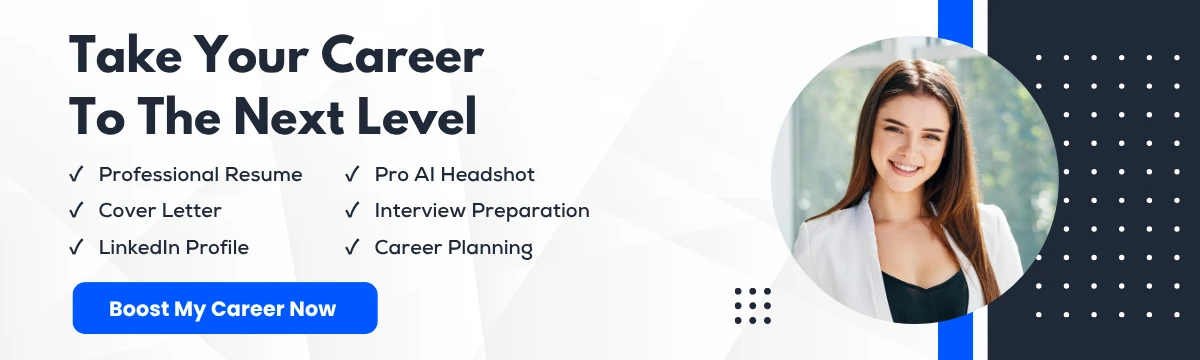
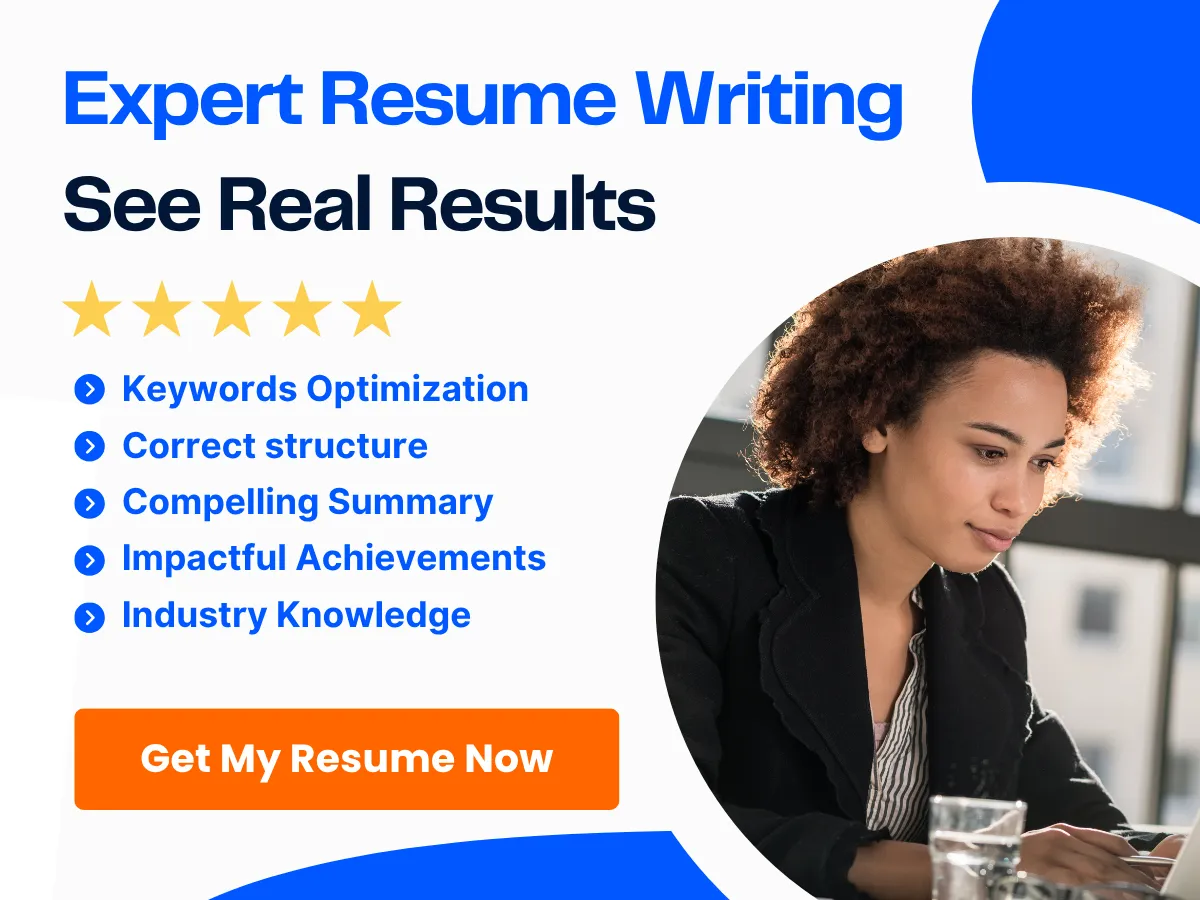
Educational Pathways
Required Educational Qualifications
To embark on a career as an instrumentation engineer, a solid educational foundation is essential. Most employers require candidates to possess at least a bachelor’s degree in engineering, with a focus on instrumentation, electrical, or control engineering. This educational background provides the necessary theoretical knowledge and practical skills needed to design, develop, and maintain instrumentation systems.
In addition to a bachelor’s degree, many instrumentation engineers pursue further education to enhance their expertise and career prospects. A master’s degree in engineering or a related field can be beneficial, especially for those looking to specialize in advanced instrumentation technologies or to take on leadership roles within their organizations. Graduate programs often delve deeper into topics such as process control, automation, and systems engineering, equipping students with a more comprehensive understanding of the field.
Relevant Degrees and Certifications
While a bachelor’s degree is the minimum requirement, certain degrees can significantly enhance an instrumentation engineer’s qualifications. Degrees in the following areas are particularly relevant:
- Electrical Engineering: This degree covers the fundamentals of electrical systems, circuits, and electronics, which are crucial for understanding instrumentation.
- Control Engineering: Focused on the design and implementation of control systems, this degree is highly relevant for instrumentation engineers who work with automated processes.
- Mechanical Engineering: While not directly related, a mechanical engineering degree can provide valuable insights into the physical systems that instrumentation engineers often work with.
- Instrumentation Engineering: Some universities offer specialized programs in instrumentation engineering, which cover topics such as sensors, measurement techniques, and control systems in depth.
In addition to formal degrees, obtaining professional certifications can further validate an engineer’s expertise and commitment to the field. Some of the most recognized certifications include:
- Certified Automation Professional (CAP): Offered by the International Society of Automation (ISA), this certification demonstrates proficiency in automation and control systems.
- Control Systems Technician (CST): Also provided by ISA, this certification is aimed at technicians who work with control systems and instrumentation.
- Project Management Professional (PMP): For those looking to advance into project management roles, the PMP certification can be invaluable, showcasing skills in managing complex engineering projects.
Specialized Courses and Training Programs
In addition to formal education and certifications, specialized courses and training programs can provide instrumentation engineers with the specific skills and knowledge needed to excel in their roles. These programs often focus on the latest technologies and methodologies in the field, ensuring that engineers remain competitive in a rapidly evolving industry.
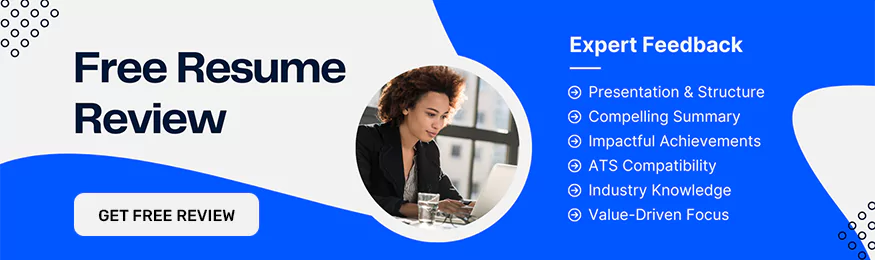
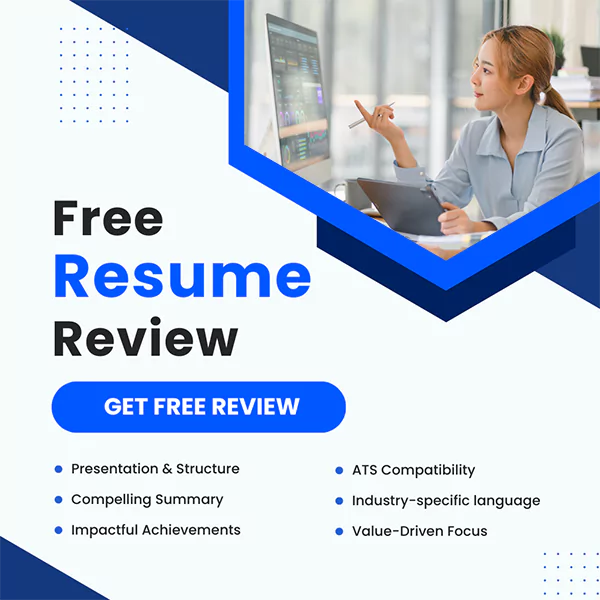
Some key areas of specialization include:
- Process Control: Courses in process control teach engineers how to design and implement control systems that regulate industrial processes. Topics may include PID control, advanced control strategies, and process optimization.
- Instrumentation and Measurement: These courses cover the principles of measurement and the operation of various types of sensors and instruments. Engineers learn about calibration, data acquisition, and signal processing.
- Industrial Automation: With the rise of Industry 4.0, courses in industrial automation focus on integrating advanced technologies such as IoT, robotics, and artificial intelligence into instrumentation systems.
- Safety Instrumented Systems (SIS): Specialized training in SIS is crucial for engineers working in industries where safety is paramount, such as oil and gas or chemical manufacturing. These courses cover the design and implementation of safety systems that protect personnel and equipment.
Many universities and technical institutes offer these specialized courses, often in partnership with industry organizations. Online platforms also provide flexible learning options, allowing engineers to enhance their skills while balancing work commitments. Popular online learning platforms include Coursera, edX, and Udacity, which offer courses from reputable institutions and industry experts.
Internships and co-op programs are also invaluable for aspiring instrumentation engineers. These opportunities provide hands-on experience in real-world settings, allowing students to apply their theoretical knowledge and gain insights into the daily operations of instrumentation engineering. Many universities have partnerships with local industries, facilitating internships that can lead to job offers upon graduation.
Continuing education is vital in the field of instrumentation engineering, as technology and industry standards are constantly evolving. Engineers are encouraged to participate in workshops, seminars, and conferences to stay updated on the latest trends and advancements. Professional organizations, such as the ISA and the Institute of Electrical and Electronics Engineers (IEEE), often host events that provide networking opportunities and access to cutting-edge research.
The educational pathways for instrumentation engineers are diverse and multifaceted. A combination of formal education, relevant degrees, certifications, specialized training, and practical experience equips engineers with the skills necessary to thrive in this dynamic field. As industries continue to embrace automation and advanced technologies, the demand for skilled instrumentation engineers is expected to grow, making this an exciting and rewarding career choice.
Core Responsibilities of an Instrumentation Engineer
Instrumentation engineers play a crucial role in various industries, including manufacturing, oil and gas, pharmaceuticals, and environmental monitoring. Their expertise lies in the design, development, installation, and maintenance of instruments that measure and control physical quantities such as pressure, temperature, flow, and level. This section delves into the core responsibilities of an instrumentation engineer, highlighting the essential tasks they perform to ensure systems operate efficiently and safely.
Designing and Developing Instrumentation Systems
One of the primary responsibilities of an instrumentation engineer is to design and develop instrumentation systems tailored to specific industrial applications. This process begins with understanding the requirements of the project, which may involve collaborating with other engineering disciplines, such as mechanical and electrical engineers, to ensure a comprehensive approach to system design.

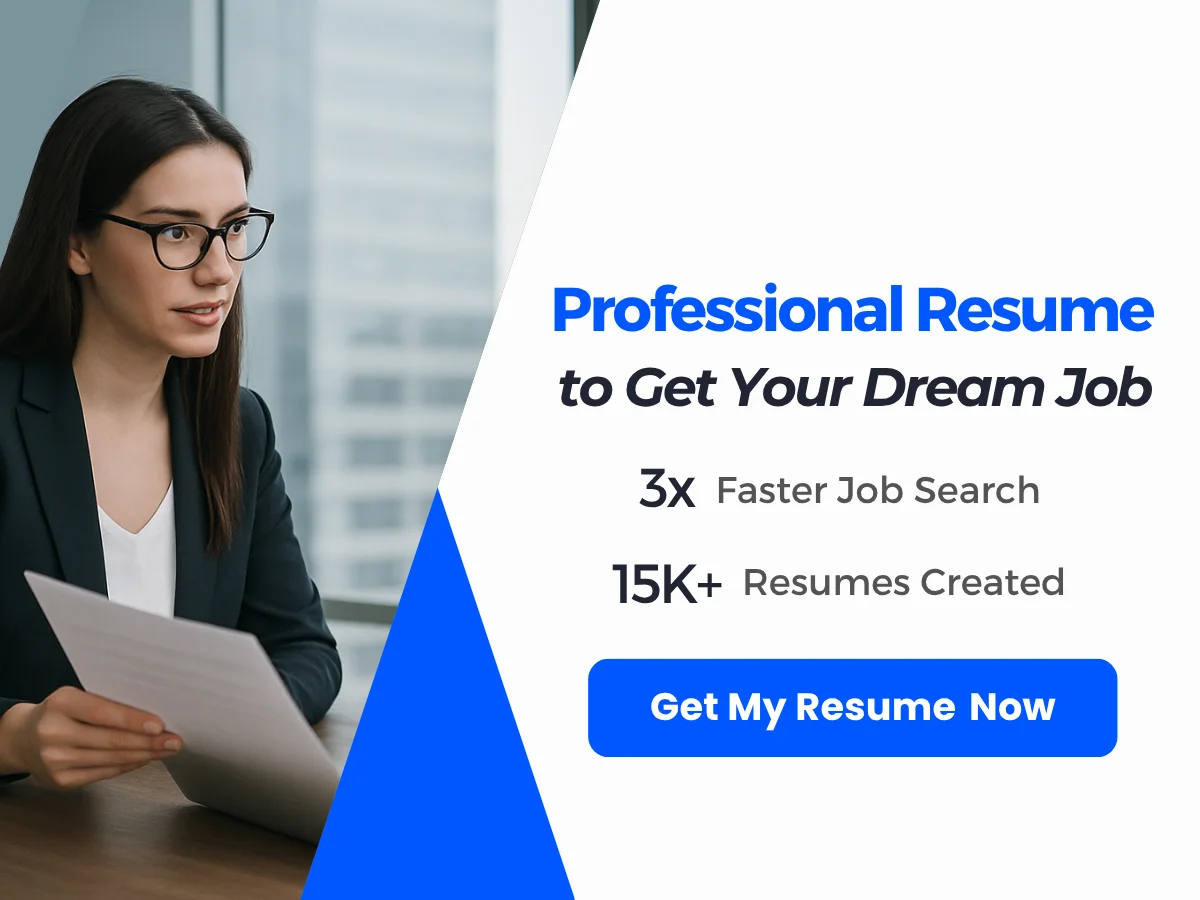
Instrumentation engineers utilize various software tools for system design, including Computer-Aided Design (CAD) software and simulation tools. They create detailed schematics and diagrams that outline the layout of instruments, control systems, and data acquisition systems. For example, in a chemical processing plant, an instrumentation engineer might design a system that includes sensors for monitoring temperature and pressure, along with control valves that regulate the flow of materials.
Moreover, instrumentation engineers must select appropriate instruments based on factors such as accuracy, range, and environmental conditions. They often conduct feasibility studies and cost analyses to determine the most effective solutions. This phase of the engineering process is critical, as it lays the foundation for the entire instrumentation system.
Installation and Calibration of Instruments
Once the design phase is complete, instrumentation engineers oversee the installation of the instrumentation systems. This involves coordinating with contractors and technicians to ensure that instruments are installed correctly and in accordance with the design specifications. Proper installation is vital to the accuracy and reliability of the measurement systems.
After installation, calibration is performed to ensure that the instruments provide accurate readings. Calibration involves comparing the instrument’s output to a known standard and making necessary adjustments. For instance, if a pressure sensor is installed in a pipeline, the instrumentation engineer will calibrate it using a pressure gauge to ensure that the readings are accurate within specified tolerances.
Instrumentation engineers also develop calibration procedures and documentation, which are essential for maintaining the integrity of the measurement systems over time. Regular calibration is necessary to account for factors such as drift, wear, and environmental changes that can affect instrument performance.
Maintenance and Troubleshooting
Maintenance is a critical aspect of an instrumentation engineer’s role. They are responsible for developing and implementing maintenance schedules to ensure that all instruments and systems remain operational. This includes routine inspections, preventive maintenance, and repairs as needed.
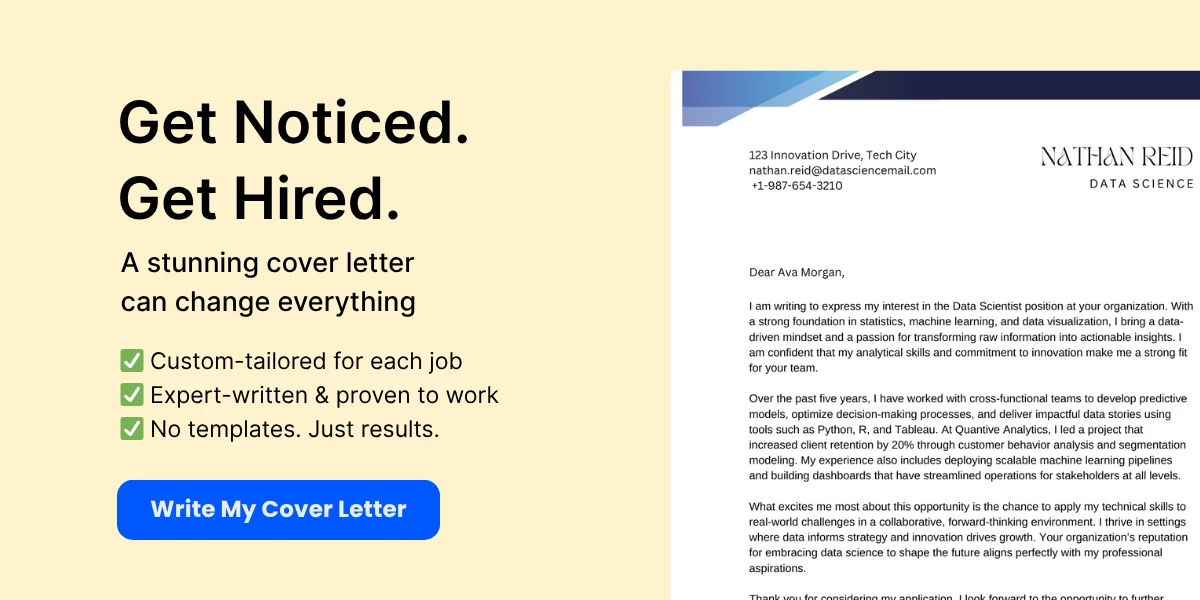
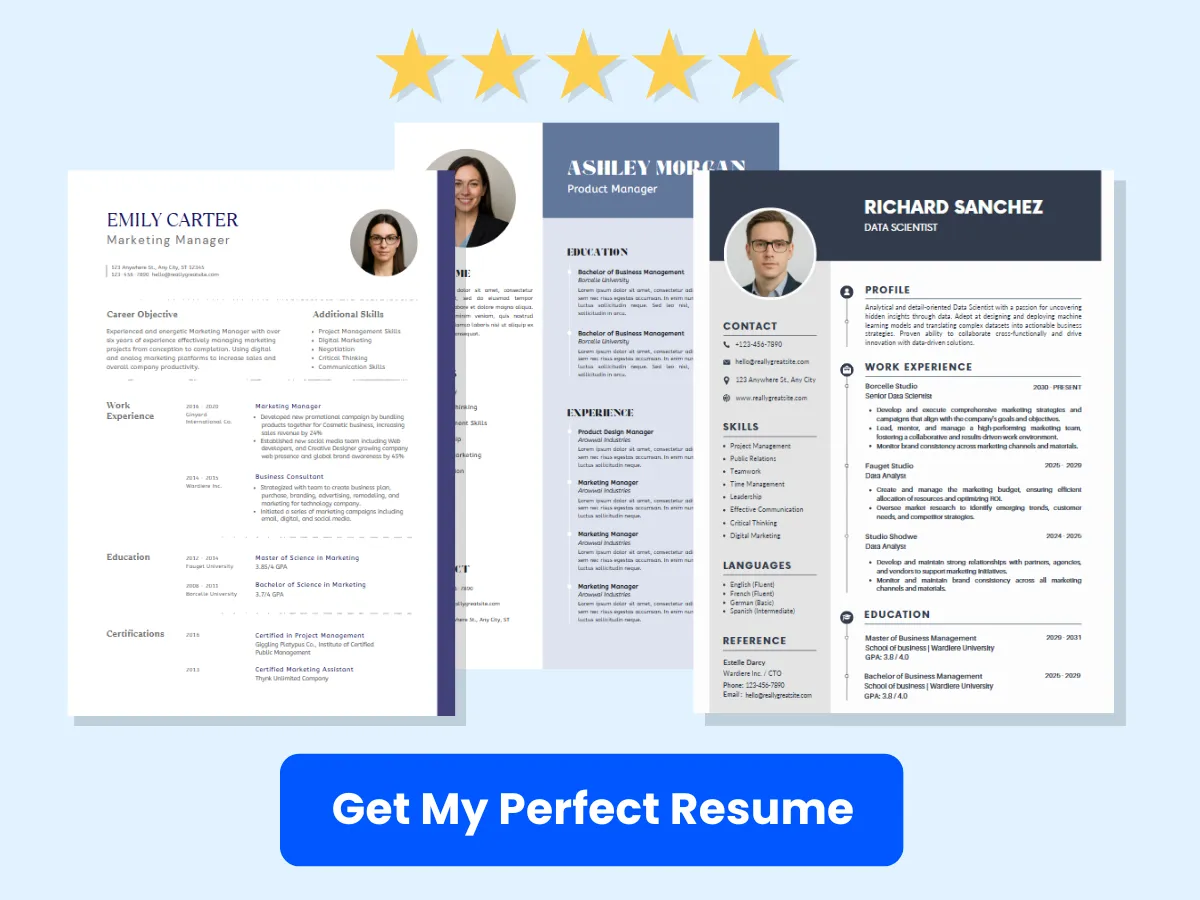
Instrumentation engineers must be adept at troubleshooting issues that arise with instrumentation systems. This requires a deep understanding of the instruments and systems in use, as well as the ability to analyze data and identify potential problems. For example, if a flow meter is providing inconsistent readings, the instrumentation engineer will investigate the issue, which may involve checking for blockages, verifying calibration, or examining the electrical connections.
Effective troubleshooting often involves using diagnostic tools and software to analyze system performance. Instrumentation engineers may also collaborate with other engineering teams to resolve complex issues that require interdisciplinary knowledge.
Data Analysis and Interpretation
Instrumentation engineers are not only responsible for the physical instruments but also for the data they generate. They analyze and interpret data collected from various sensors and instruments to provide insights that can improve operational efficiency and safety. This analysis often involves using statistical methods and software tools to process large datasets.
For instance, in a manufacturing environment, an instrumentation engineer may analyze temperature and pressure data from a production line to identify trends and anomalies. By interpreting this data, they can recommend adjustments to the process to enhance productivity or reduce waste.
Furthermore, instrumentation engineers often prepare reports and presentations to communicate their findings to stakeholders, including management and other engineering teams. This aspect of their role is crucial for informed decision-making and continuous improvement within the organization.
Ensuring Compliance with Safety and Regulatory Standards
Safety and regulatory compliance are paramount in the field of instrumentation engineering. Engineers must ensure that all instrumentation systems adhere to industry standards and regulations, which vary by sector and region. This includes understanding and implementing standards set by organizations such as the International Society of Automation (ISA), the American National Standards Institute (ANSI), and the Occupational Safety and Health Administration (OSHA).
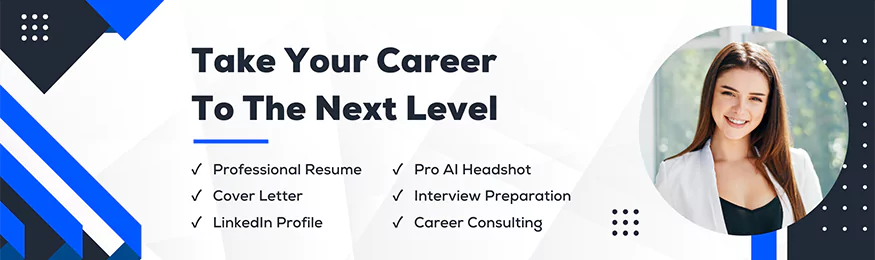
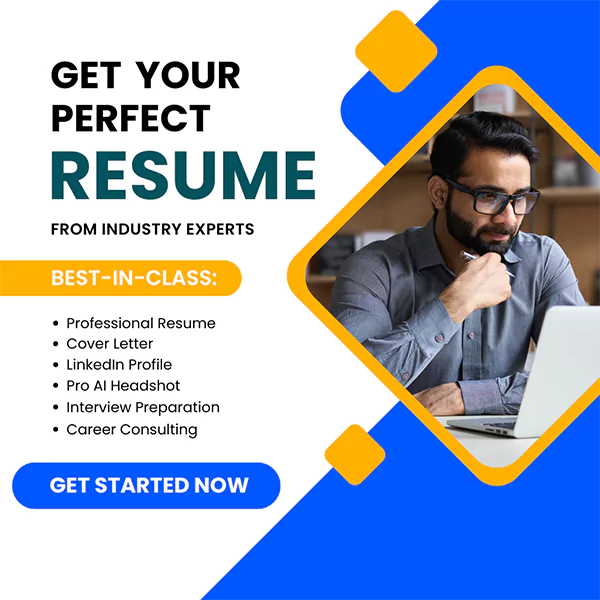
Instrumentation engineers conduct risk assessments to identify potential hazards associated with instrumentation systems and develop strategies to mitigate these risks. For example, in the oil and gas industry, they may implement safety measures to prevent leaks or explosions by ensuring that pressure relief valves and other safety instruments are functioning correctly.
Additionally, instrumentation engineers are often involved in audits and inspections to verify compliance with safety regulations. They may also provide training to personnel on the proper use and maintenance of instrumentation systems, emphasizing the importance of safety protocols and procedures.
The role of an instrumentation engineer encompasses a wide range of responsibilities, from designing and developing instrumentation systems to ensuring compliance with safety standards. Their expertise is vital in maintaining the efficiency and safety of industrial processes, making them an integral part of any engineering team.
Key Skills and Competencies
Instrumentation engineering is a multifaceted discipline that requires a diverse set of skills and competencies. Professionals in this field must possess a blend of technical knowledge, practical abilities, and interpersonal skills to effectively design, implement, and maintain instrumentation systems. Below, we delve into the key skills and competencies that define a successful instrumentation engineer.
Technical Skills
At the core of an instrumentation engineer’s role are the technical skills that enable them to understand and manipulate various instruments and systems. This includes a strong foundation in electrical and electronic engineering principles, as well as a deep understanding of the specific instruments used in measurement and control processes.
Instrumentation engineers must be proficient in the following technical areas:
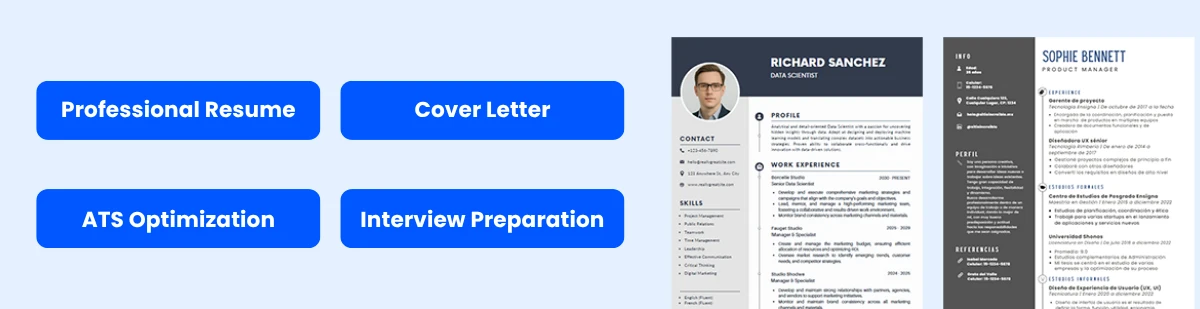
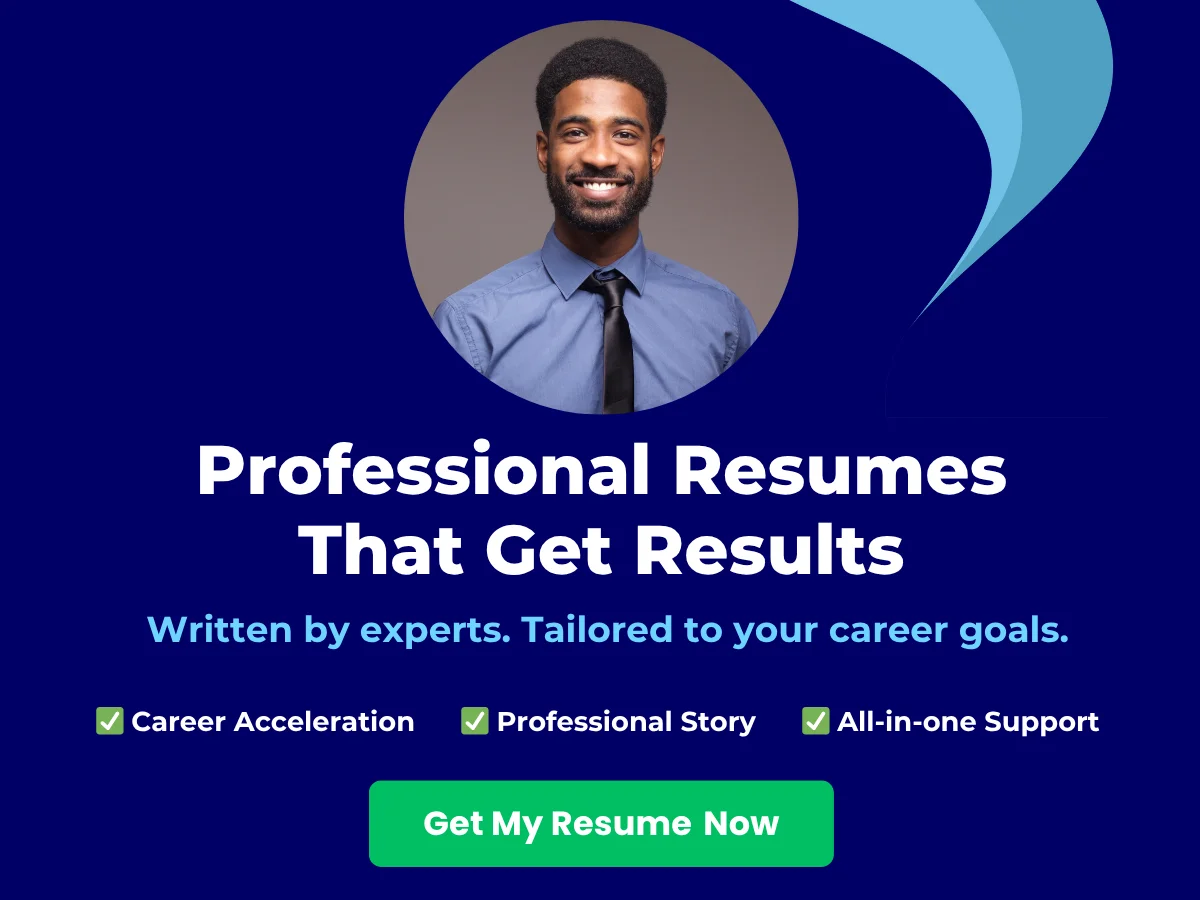
- Measurement Techniques: Understanding how to accurately measure physical quantities such as temperature, pressure, flow, and level is crucial. Engineers must be familiar with different measurement techniques and the instruments used, such as thermocouples, pressure transducers, and flow meters.
- Calibration: The ability to calibrate instruments to ensure accuracy and reliability is essential. This involves adjusting the instrument to provide correct readings and understanding the standards and procedures for calibration.
- Data Acquisition: Knowledge of data acquisition systems and how to collect, store, and analyze data from various sensors is vital. Engineers often work with software tools that facilitate data logging and analysis.
Knowledge of Sensors and Transducers
Sensors and transducers are the backbone of instrumentation systems. An instrumentation engineer must have a comprehensive understanding of various types of sensors, their operating principles, and their applications. This includes:
- Types of Sensors: Familiarity with different sensor types, such as resistive, capacitive, inductive, and optical sensors, is necessary. Each type has its unique characteristics, advantages, and limitations.
- Transducer Functionality: Understanding how transducers convert physical phenomena into electrical signals is crucial. Engineers must know how to select the appropriate transducer for a specific application based on factors like range, sensitivity, and environmental conditions.
- Integration with Systems: Knowledge of how to integrate sensors and transducers into larger control systems is essential. This includes understanding signal conditioning, amplification, and filtering processes.
Proficiency in Control Systems and Automation
Instrumentation engineers often work closely with control systems and automation technologies. Proficiency in these areas is critical for designing systems that can automatically regulate processes based on sensor inputs. Key aspects include:
- Control Theory: A solid grasp of control theory principles, including feedback loops, PID controllers, and stability analysis, is necessary for designing effective control systems.
- Programmable Logic Controllers (PLCs): Familiarity with PLC programming and operation is essential, as these devices are widely used in industrial automation to control machinery and processes.
- SCADA Systems: Knowledge of Supervisory Control and Data Acquisition (SCADA) systems is important for monitoring and controlling industrial processes remotely.
Exploring Signal Processing
Signal processing is a critical skill for instrumentation engineers, as it involves the analysis and manipulation of signals obtained from sensors. This includes:
- Signal Conditioning: Understanding how to enhance the quality of signals through filtering, amplification, and noise reduction techniques is vital for accurate measurements.
- Data Analysis: Proficiency in data analysis techniques, including statistical methods and algorithms, allows engineers to interpret sensor data effectively and make informed decisions.
- Software Tools: Familiarity with software tools for signal processing, such as MATLAB or LabVIEW, is often required to simulate and analyze system performance.
Soft Skills
While technical skills are paramount, soft skills play a significant role in the effectiveness of an instrumentation engineer. These skills facilitate collaboration, communication, and project execution. Key soft skills include:
Problem-Solving Abilities
Instrumentation engineers frequently encounter complex challenges that require innovative solutions. Strong problem-solving abilities enable them to:
- Diagnose Issues: Quickly identify and analyze problems within instrumentation systems, whether they are related to hardware malfunctions or software bugs.
- Develop Solutions: Create effective solutions that address the root cause of issues, often requiring creative thinking and a deep understanding of the systems involved.
- Implement Changes: Effectively implement changes to improve system performance or rectify issues, ensuring minimal disruption to operations.
Communication and Teamwork
Instrumentation engineers often work in multidisciplinary teams, collaborating with professionals from various fields such as mechanical engineering, software development, and project management. Effective communication and teamwork skills are essential for:
- Sharing Ideas: Clearly articulating technical concepts and ideas to team members and stakeholders, ensuring everyone is on the same page.
- Collaborating on Projects: Working effectively with others to achieve project goals, leveraging the diverse skills and perspectives of team members.
- Training and Mentoring: Providing guidance and support to junior engineers or technicians, fostering a collaborative learning environment.
Project Management
Instrumentation engineers often take on project management responsibilities, requiring them to possess strong organizational and leadership skills. Key aspects of project management in instrumentation engineering include:
- Planning and Scheduling: Developing project plans that outline timelines, resources, and milestones, ensuring projects are completed on time and within budget.
- Resource Management: Effectively managing resources, including personnel, equipment, and materials, to optimize project outcomes.
- Risk Management: Identifying potential risks and developing mitigation strategies to minimize their impact on project success.
The role of an instrumentation engineer is multifaceted, requiring a combination of technical expertise, knowledge of systems and components, and strong interpersonal skills. By mastering these key skills and competencies, instrumentation engineers can effectively contribute to the design, implementation, and maintenance of complex instrumentation systems across various industries.
Tools and Technologies Used
Software Tools
Instrumentation engineers rely heavily on a variety of software tools to design, analyze, and implement measurement systems. These tools facilitate the simulation of systems, data analysis, and the development of control algorithms. Below are some of the most commonly used software tools in the field:
- MATLAB: MATLAB is a high-level programming language and interactive environment used for numerical computation, visualization, and programming. Instrumentation engineers use MATLAB for data analysis, algorithm development, and modeling of dynamic systems. Its extensive libraries and toolboxes, such as the Control System Toolbox and Signal Processing Toolbox, allow engineers to simulate and analyze complex systems efficiently.
- LabVIEW: LabVIEW (Laboratory Virtual Instrument Engineering Workbench) is a system-design platform and development environment for a visual programming language. It is widely used in instrumentation for data acquisition, instrument control, and industrial automation. LabVIEW allows engineers to create user-friendly interfaces and automate testing processes, making it an essential tool for instrumentation engineers working in research and development or quality assurance.
- SPICE: SPICE (Simulation Program with Integrated Circuit Emphasis) is a powerful tool for simulating electronic circuits. Instrumentation engineers use SPICE to analyze the behavior of circuits under various conditions, helping them design more effective measurement systems. By simulating circuits before physical implementation, engineers can identify potential issues and optimize performance.
- AutoCAD: While primarily known for its applications in architecture and engineering design, AutoCAD is also used by instrumentation engineers for creating detailed schematics and layouts of instrumentation systems. This software helps in visualizing the physical arrangement of instruments and ensuring that all components fit together correctly.
- Python: Python has gained popularity in the instrumentation field due to its simplicity and versatility. Engineers use Python for data analysis, automation of measurement processes, and integration with hardware. Libraries such as NumPy and Pandas facilitate data manipulation, while Matplotlib and Seaborn are used for data visualization.
Hardware Tools
In addition to software, instrumentation engineers utilize a variety of hardware tools to measure, analyze, and control physical quantities. These tools are essential for the practical implementation of instrumentation systems. Some of the key hardware tools include:
- Oscilloscopes: Oscilloscopes are vital for visualizing electrical signals. They allow engineers to observe the waveform of signals over time, making it easier to analyze the behavior of electronic circuits and systems. By providing real-time data, oscilloscopes help engineers troubleshoot issues and ensure that systems operate within specified parameters.
- Multimeters: Multimeters are essential for measuring voltage, current, and resistance in electrical circuits. They are used extensively in both laboratory and field settings to verify the performance of instrumentation systems. Advanced multimeters can also measure frequency, capacitance, and temperature, making them versatile tools for instrumentation engineers.
- Signal Generators: Signal generators produce electrical signals of varying frequencies and amplitudes. They are used to test and calibrate instrumentation systems by simulating real-world conditions. Engineers can use signal generators to assess the response of their systems to different input signals, ensuring accuracy and reliability.
- Data Acquisition Systems (DAQ): DAQ systems are used to collect, measure, and analyze data from various sensors and instruments. These systems convert analog signals into digital data that can be processed by computers. Instrumentation engineers use DAQ systems to monitor and control processes in real-time, making them crucial for applications in research, manufacturing, and environmental monitoring.
- Transducers and Sensors: Transducers and sensors are fundamental components of any instrumentation system. They convert physical quantities (such as temperature, pressure, or flow) into electrical signals that can be measured and analyzed. Instrumentation engineers select appropriate sensors based on the specific requirements of their applications, ensuring accurate and reliable measurements.
Emerging Technologies
The field of instrumentation engineering is rapidly evolving, with emerging technologies playing a significant role in shaping the future of measurement and control systems. Some of the most notable trends include:
- Internet of Things (IoT): The IoT refers to the interconnection of everyday devices to the internet, allowing them to send and receive data. In instrumentation, IoT enables remote monitoring and control of systems, providing real-time data access and analysis. Instrumentation engineers are increasingly integrating IoT technologies into their designs, allowing for smarter and more efficient systems. For example, IoT-enabled sensors can monitor environmental conditions and send alerts when parameters exceed predefined thresholds, enhancing safety and efficiency in industrial applications.
- Artificial Intelligence (AI) in Instrumentation: AI technologies are being integrated into instrumentation systems to enhance data analysis and decision-making processes. Machine learning algorithms can analyze large datasets to identify patterns and anomalies, enabling predictive maintenance and improved system performance. For instance, AI can be used to predict equipment failures before they occur, allowing for timely interventions and reducing downtime.
- Big Data Analytics: The increasing volume of data generated by instrumentation systems necessitates advanced analytics techniques. Instrumentation engineers are leveraging big data analytics to extract meaningful insights from complex datasets. This capability allows for better decision-making and optimization of processes in various industries, including manufacturing, healthcare, and environmental monitoring.
- Wireless Technologies: Wireless communication technologies, such as Bluetooth, Wi-Fi, and cellular networks, are transforming the way instrumentation systems operate. Wireless sensors and devices enable greater flexibility and mobility in data collection and monitoring. Instrumentation engineers are adopting these technologies to create more efficient and scalable systems, particularly in remote or hard-to-reach locations.
- Advanced Materials: The development of advanced materials, such as nanomaterials and smart materials, is opening new possibilities for instrumentation. These materials can enhance the sensitivity and accuracy of sensors, leading to improved measurement capabilities. Instrumentation engineers are exploring the use of these materials to create next-generation sensors that can operate in extreme conditions or provide real-time feedback on structural health.
As instrumentation engineering continues to evolve, the integration of these tools and technologies will play a crucial role in enhancing the capabilities and efficiency of measurement systems. By staying abreast of these advancements, instrumentation engineers can ensure that they are well-equipped to meet the challenges of modern engineering and contribute to the development of innovative solutions across various industries.
Industries and Applications
Instrumentation engineers play a crucial role across various industries, ensuring that processes are efficient, safe, and compliant with regulations. Their expertise in measurement, control, and automation is vital in sectors where precision and reliability are paramount. Below, we explore the key industries where instrumentation engineers are essential, detailing their specific applications and contributions.
Oil and Gas
The oil and gas industry is one of the most significant sectors for instrumentation engineers. They are involved in the exploration, extraction, refining, and distribution of oil and gas products. Instrumentation engineers design and maintain systems that monitor and control the various processes involved in this industry.
For instance, in upstream operations, instrumentation engineers work on drilling rigs and production platforms, where they implement sensors and control systems to monitor pressure, temperature, and flow rates of oil and gas. These measurements are critical for ensuring safe operations and optimizing production rates. In downstream operations, such as refineries, they focus on process control systems that manage the complex chemical processes involved in refining crude oil into usable products like gasoline and diesel.
Moreover, instrumentation engineers are responsible for ensuring compliance with safety and environmental regulations. They design systems that detect leaks, monitor emissions, and ensure that operations do not harm the environment. Advanced technologies such as SCADA (Supervisory Control and Data Acquisition) systems are often employed to provide real-time data and control over large geographical areas, enhancing operational efficiency and safety.
Manufacturing and Production
In the manufacturing sector, instrumentation engineers are integral to the automation and control of production processes. They work on a variety of systems, from assembly lines to complex manufacturing plants, ensuring that machinery operates efficiently and produces high-quality products.
Instrumentation engineers design and implement control systems that utilize sensors, actuators, and controllers to automate processes. For example, in a car manufacturing plant, they may develop systems that monitor the assembly line’s speed, ensuring that each component is assembled correctly and on time. They also work on quality control systems that use sensors to detect defects in products, allowing for immediate corrective actions.
Additionally, instrumentation engineers are involved in the integration of Industry 4.0 technologies, such as the Internet of Things (IoT) and artificial intelligence (AI), into manufacturing processes. These technologies enable real-time data collection and analysis, leading to smarter decision-making and predictive maintenance, which can significantly reduce downtime and operational costs.
Pharmaceuticals and Biotechnology
The pharmaceutical and biotechnology industries require stringent control and monitoring of processes to ensure product quality and compliance with regulatory standards. Instrumentation engineers in these fields focus on developing and maintaining systems that monitor critical parameters such as temperature, pressure, pH, and flow rates during drug production.
For example, in the production of vaccines or biologics, instrumentation engineers design systems that ensure sterile conditions and precise control over the fermentation processes. They implement advanced monitoring systems that provide real-time data on the growth conditions of microorganisms, which is essential for optimizing yields and ensuring product safety.
Moreover, instrumentation engineers are involved in the validation of processes and equipment, ensuring that they meet the stringent requirements set by regulatory bodies such as the FDA (Food and Drug Administration). This includes developing protocols for equipment calibration, maintenance, and performance verification, which are critical for maintaining compliance and ensuring patient safety.
Aerospace and Defense
In the aerospace and defense sectors, instrumentation engineers are responsible for the design and implementation of systems that ensure the safety and reliability of aircraft and defense systems. They work on a variety of applications, from avionics systems in commercial aircraft to missile guidance systems in defense applications.
Instrumentation engineers develop and maintain systems that monitor critical parameters such as altitude, speed, and engine performance. For instance, in an aircraft, they may work on the flight control systems that utilize sensors to provide real-time data to pilots, ensuring safe and efficient operation. They also work on testing and validation processes to ensure that all systems meet rigorous safety standards.
In defense applications, instrumentation engineers are involved in the development of advanced systems for surveillance, reconnaissance, and targeting. They design sensors and control systems that provide accurate data for decision-making in complex and high-stakes environments. The integration of cutting-edge technologies such as radar, GPS, and advanced imaging systems is a key focus area for instrumentation engineers in this sector.
Environmental Monitoring
Environmental monitoring is another critical area where instrumentation engineers make significant contributions. They design and implement systems that monitor air and water quality, track pollution levels, and ensure compliance with environmental regulations.
For example, instrumentation engineers may develop systems that utilize sensors to measure pollutants in the air, such as carbon dioxide, sulfur dioxide, and particulate matter. These systems provide real-time data that can be used by regulatory agencies to enforce environmental laws and protect public health.
In water quality monitoring, instrumentation engineers design systems that measure parameters such as pH, turbidity, and dissolved oxygen levels in rivers, lakes, and treatment plants. This data is essential for ensuring safe drinking water and maintaining healthy ecosystems. They also work on developing automated sampling systems that can collect water samples for laboratory analysis, enhancing the efficiency of environmental monitoring programs.
Furthermore, instrumentation engineers are involved in the development of technologies for renewable energy sources, such as wind and solar power. They design monitoring systems that track the performance of renewable energy installations, ensuring that they operate efficiently and contribute to sustainable energy goals.
Instrumentation engineers are vital across a wide range of industries, from oil and gas to environmental monitoring. Their expertise in measurement, control, and automation ensures that processes are efficient, safe, and compliant with regulations. As technology continues to evolve, the role of instrumentation engineers will only become more critical in driving innovation and sustainability across these sectors.
Career Opportunities and Job Roles
Entry-Level Positions
For those embarking on a career as an instrumentation engineer, entry-level positions serve as the foundation for professional growth and skill development. Typically, recent graduates with a degree in instrumentation engineering, electrical engineering, or a related field can expect to start in roles such as:
- Instrumentation Technician: In this role, individuals assist in the installation, maintenance, and calibration of instruments and control systems. They work under the supervision of senior engineers, gaining hands-on experience with various types of instrumentation.
- Junior Instrumentation Engineer: This position involves supporting senior engineers in designing and implementing instrumentation systems. Responsibilities may include drafting technical documentation, conducting tests, and analyzing data.
- Field Service Engineer: Entry-level field service engineers travel to client sites to troubleshoot and repair instrumentation equipment. This role requires strong problem-solving skills and the ability to work independently.
These positions often provide exposure to real-world applications of instrumentation engineering, allowing new professionals to develop essential skills in system design, troubleshooting, and project management. Many companies also offer training programs to help entry-level employees gain the necessary technical knowledge and industry insights.
Mid-Level and Senior Positions
As instrumentation engineers gain experience, they can advance to mid-level and senior positions, where they take on more complex projects and leadership roles. Common job titles at this level include:
- Instrumentation Engineer: Mid-level engineers are responsible for designing, developing, and implementing instrumentation systems. They collaborate with other engineering disciplines to ensure that systems meet project specifications and regulatory requirements.
- Lead Instrumentation Engineer: In this role, engineers oversee project teams, manage budgets, and ensure that projects are completed on time. They are also responsible for mentoring junior engineers and technicians.
- Project Manager: Experienced instrumentation engineers may transition into project management roles, where they coordinate all aspects of instrumentation projects, from initial design to final implementation. This position requires strong leadership and communication skills, as well as a deep understanding of engineering principles.
Mid-level and senior positions often require a combination of technical expertise and soft skills, such as teamwork, communication, and problem-solving. Engineers at this level are expected to lead projects, make critical decisions, and ensure compliance with industry standards.
Specialized Roles
Instrumentation engineering is a diverse field, and many professionals choose to specialize in specific areas to enhance their career prospects. Some specialized roles include:
- Control Systems Engineer: These engineers focus on designing and implementing control systems that regulate processes in industries such as manufacturing, oil and gas, and pharmaceuticals. They work with programmable logic controllers (PLCs), distributed control systems (DCS), and other automation technologies to optimize system performance.
- Automation Engineer: Automation engineers design and implement automated systems that improve efficiency and reduce human intervention in processes. They work closely with instrumentation engineers to integrate sensors, actuators, and control systems into automated solutions.
- Process Control Engineer: This role involves optimizing industrial processes through the use of instrumentation and control systems. Process control engineers analyze data, develop control strategies, and implement changes to improve process efficiency and product quality.
Specialization allows instrumentation engineers to deepen their expertise in specific technologies or industries, making them more valuable to employers and increasing their earning potential. Many companies encourage specialization by providing training and development opportunities in emerging technologies.
Freelance and Consultancy Opportunities
With the rise of the gig economy and the increasing demand for specialized skills, many instrumentation engineers are exploring freelance and consultancy opportunities. This path offers flexibility and the chance to work on diverse projects across various industries. Freelance instrumentation engineers may provide services such as:
- System Design and Implementation: Freelancers can assist companies in designing and implementing instrumentation systems tailored to their specific needs. This may involve conducting site assessments, developing specifications, and overseeing installation.
- Training and Support: Experienced engineers can offer training programs for companies looking to upskill their staff in instrumentation technologies and best practices. This can include workshops, seminars, and one-on-one coaching.
- Consulting Services: Instrumentation engineers can work as consultants, providing expert advice on system optimization, regulatory compliance, and technology selection. This role often requires a deep understanding of industry standards and best practices.
Freelancing and consultancy can be rewarding for instrumentation engineers who enjoy variety in their work and the opportunity to collaborate with different clients. However, it also requires strong self-management skills, as engineers must handle their own marketing, client relations, and project management.
Challenges and Future Trends
Current Challenges in the Field
Instrumentation engineering is a dynamic field that plays a crucial role in various industries, including manufacturing, oil and gas, pharmaceuticals, and environmental monitoring. However, professionals in this domain face several challenges that can impact their work and the overall effectiveness of instrumentation systems.
1. Rapid Technological Changes
One of the most significant challenges for instrumentation engineers is keeping pace with rapid technological advancements. The field is constantly evolving, with new tools, techniques, and methodologies emerging regularly. Engineers must continuously update their skills and knowledge to remain relevant. This can involve attending workshops, pursuing further education, or obtaining certifications in new technologies.
2. Integration of Systems
As industries adopt more complex systems, the integration of various instrumentation components becomes increasingly challenging. Engineers must ensure that different devices, sensors, and control systems work seamlessly together. This requires a deep understanding of both hardware and software, as well as the ability to troubleshoot and resolve compatibility issues.
3. Data Management and Analysis
With the rise of the Internet of Things (IoT) and big data, instrumentation engineers are now tasked with managing vast amounts of data generated by sensors and devices. Analyzing this data to derive actionable insights is crucial for optimizing processes and improving efficiency. However, the sheer volume of data can be overwhelming, and engineers must develop robust data management strategies to handle it effectively.
4. Regulatory Compliance
Instrumentation engineers often work in highly regulated industries, such as pharmaceuticals and food processing, where compliance with safety and quality standards is paramount. Navigating these regulations can be complex and time-consuming. Engineers must stay informed about the latest regulations and ensure that their instrumentation systems meet all necessary requirements.
5. Cybersecurity Threats
As instrumentation systems become more interconnected, they also become more vulnerable to cyberattacks. Engineers must implement robust cybersecurity measures to protect sensitive data and ensure the integrity of their systems. This includes regular software updates, network security protocols, and employee training on cybersecurity best practices.
Impact of Technological Advancements
Technological advancements have significantly transformed the field of instrumentation engineering, leading to improved efficiency, accuracy, and safety in various applications. Here are some key areas where technology has made a substantial impact:
1. Smart Sensors and IoT
The advent of smart sensors and IoT technology has revolutionized the way data is collected and analyzed. Smart sensors can communicate with each other and transmit data in real-time, allowing for more responsive and adaptive systems. For example, in a manufacturing plant, smart sensors can monitor equipment performance and alert engineers to potential issues before they lead to costly downtime.
2. Advanced Data Analytics
With the integration of advanced data analytics tools, instrumentation engineers can now analyze large datasets to identify trends, predict failures, and optimize processes. Machine learning algorithms can be employed to enhance predictive maintenance strategies, reducing the likelihood of unexpected equipment failures and improving overall operational efficiency.
3. Automation and Control Systems
Automation has become a cornerstone of modern instrumentation engineering. Engineers are increasingly tasked with designing and implementing automated control systems that can operate independently or with minimal human intervention. This not only improves efficiency but also enhances safety by reducing the risk of human error. For instance, in chemical processing plants, automated control systems can monitor and adjust parameters in real-time to maintain optimal operating conditions.
4. Remote Monitoring and Diagnostics
Technological advancements have enabled remote monitoring and diagnostics of instrumentation systems. Engineers can now access data and control systems from anywhere in the world, allowing for quicker response times and more efficient troubleshooting. This is particularly beneficial in industries such as oil and gas, where equipment is often located in remote areas.
5. Enhanced Visualization Tools
Modern visualization tools allow engineers to create intuitive dashboards and graphical representations of data, making it easier to interpret complex information. These tools can help engineers quickly identify anomalies and make informed decisions based on real-time data. For example, a visualization dashboard in a water treatment facility can display key performance indicators, enabling operators to monitor system health at a glance.
Future Trends and Innovations
The future of instrumentation engineering is poised for exciting developments, driven by ongoing technological advancements and the increasing demand for efficiency and sustainability. Here are some anticipated trends and innovations in the field:
1. Increased Use of Artificial Intelligence
Artificial intelligence (AI) is expected to play a significant role in the future of instrumentation engineering. AI algorithms can analyze data more efficiently than traditional methods, enabling engineers to make quicker and more accurate decisions. For instance, AI can be used to optimize control systems in real-time, adjusting parameters based on changing conditions to enhance performance and reduce energy consumption.
2. Greater Focus on Sustainability
As industries face increasing pressure to adopt sustainable practices, instrumentation engineers will play a critical role in developing systems that minimize environmental impact. This includes designing instrumentation for renewable energy sources, such as solar and wind, as well as implementing monitoring systems that track emissions and resource usage in real-time.
3. Expansion of Digital Twins
The concept of digital twins—virtual replicas of physical systems—will become more prevalent in instrumentation engineering. By creating digital twins, engineers can simulate and analyze the performance of systems under various conditions, allowing for better design and optimization. This technology can be particularly useful in industries such as aerospace and automotive, where precision and reliability are paramount.
4. Enhanced Cybersecurity Measures
As the threat of cyberattacks continues to grow, the importance of cybersecurity in instrumentation engineering will only increase. Future innovations will likely focus on developing more robust security protocols and technologies to protect instrumentation systems from potential breaches. This may include advanced encryption methods, intrusion detection systems, and continuous monitoring solutions.
5. Integration of Augmented and Virtual Reality
Augmented reality (AR) and virtual reality (VR) technologies are expected to find applications in instrumentation engineering, particularly in training and maintenance. Engineers can use AR to overlay digital information onto physical systems, providing real-time guidance during maintenance tasks. VR can be utilized for immersive training experiences, allowing engineers to practice troubleshooting and system operation in a safe, controlled environment.
While instrumentation engineers face numerous challenges in their field, the impact of technological advancements and the emergence of future trends present exciting opportunities for innovation and growth. By embracing these changes, instrumentation engineers can continue to enhance their contributions to various industries, driving efficiency, safety, and sustainability in their work.
Professional Development and Networking
Instrumentation engineering is a dynamic field that requires continuous learning and adaptation to new technologies and methodologies. As the industry evolves, so too must the skills and knowledge of instrumentation engineers. Professional development and networking play a crucial role in ensuring that these engineers remain at the forefront of their field. This section explores various avenues for professional growth, including professional organizations, conferences, workshops, seminars, and continuing education and certification programs.
Professional Organizations and Societies
Joining professional organizations and societies is one of the most effective ways for instrumentation engineers to enhance their careers. These organizations provide a platform for networking, knowledge sharing, and professional development. Some of the most notable organizations include:
- International Society of Automation (ISA): Founded in 1945, ISA is a global organization that focuses on advancing the technical competence of automation professionals. It offers resources such as technical publications, training programs, and certification opportunities. Membership provides access to a vast network of professionals and industry experts.
- Institute of Electrical and Electronics Engineers (IEEE): While IEEE covers a broad range of engineering disciplines, its focus on electrical and electronic engineering makes it relevant for instrumentation engineers. IEEE offers numerous resources, including journals, conferences, and local chapters that facilitate networking and collaboration.
- American Society for Quality (ASQ): ASQ is dedicated to quality improvement and offers resources that are beneficial for instrumentation engineers involved in quality control and assurance. Membership provides access to training, certifications, and a community of quality professionals.
- Society of Petroleum Engineers (SPE): For those in the oil and gas sector, SPE offers resources tailored to instrumentation engineers working in this industry. It provides networking opportunities, technical resources, and industry insights.
Being a member of these organizations not only enhances an engineer’s resume but also provides opportunities for mentorship, collaboration, and access to exclusive resources that can aid in career advancement.
Conferences, Workshops, and Seminars
Attending conferences, workshops, and seminars is another vital aspect of professional development for instrumentation engineers. These events offer a unique opportunity to learn about the latest trends, technologies, and best practices in the field. They also provide a platform for networking with peers, industry leaders, and potential employers.
Some prominent conferences and workshops include:
- ISA Automation Week: This annual event brings together automation professionals from around the world to discuss the latest advancements in instrumentation and control systems. It features technical sessions, workshops, and an exhibition showcasing the latest technologies.
- IEEE International Conference on Industrial Technology: This conference focuses on industrial technology and provides a platform for researchers and practitioners to share their findings and innovations. It covers a wide range of topics relevant to instrumentation engineering.
- Control Systems Society Conferences: Organized by the IEEE Control Systems Society, these conferences focus on control systems and automation, providing insights into the latest research and applications in the field.
- Local Workshops and Seminars: Many professional organizations host local workshops and seminars that focus on specific topics within instrumentation engineering. These events are often more accessible and provide hands-on learning opportunities.
Participating in these events not only enhances knowledge but also allows engineers to showcase their work, gain feedback, and establish connections that can lead to future collaborations or job opportunities.
Continuing Education and Certification Programs
In a rapidly changing technological landscape, continuing education is essential for instrumentation engineers to stay relevant. Many organizations offer certification programs that validate an engineer’s skills and knowledge in specific areas of instrumentation and control. Some notable certification programs include:
- Certified Automation Professional (CAP): Offered by ISA, this certification demonstrates an engineer’s expertise in automation and control systems. It covers a wide range of topics, including system design, implementation, and maintenance.
- Control Systems Technician (CST): Also provided by ISA, this certification is aimed at technicians who work with control systems. It focuses on the practical skills needed to install, maintain, and troubleshoot instrumentation and control systems.
- Project Management Professional (PMP): For instrumentation engineers involved in project management, obtaining a PMP certification can enhance their ability to lead projects effectively. This certification is recognized globally and demonstrates a commitment to project management excellence.
- Six Sigma Certification: Many instrumentation engineers work in environments where quality control is paramount. Six Sigma certifications (such as Green Belt or Black Belt) provide engineers with the tools and methodologies to improve processes and reduce defects.
In addition to formal certifications, many universities and technical institutions offer continuing education courses that cover emerging technologies and methodologies in instrumentation engineering. These courses can be taken online or in-person, providing flexibility for working professionals.
Networking Opportunities
Networking is a critical component of professional development for instrumentation engineers. Building a strong professional network can lead to job opportunities, collaborations, and mentorship. Here are some effective ways to network within the field:
- Join Online Forums and Social Media Groups: Platforms like LinkedIn, Reddit, and specialized forums provide opportunities to connect with other professionals in the field. Engaging in discussions, sharing knowledge, and asking questions can help build relationships and expand one’s network.
- Participate in Local Meetups: Many cities have local meetups for engineering professionals. These informal gatherings provide a relaxed environment for networking and sharing experiences with peers.
- Volunteer for Professional Organizations: Volunteering for committees or events within professional organizations can provide valuable networking opportunities. It allows engineers to meet industry leaders and contribute to the advancement of their field.
- Mentorship Programs: Many professional organizations offer mentorship programs that connect experienced professionals with those new to the field. Engaging in a mentorship relationship can provide guidance, support, and valuable industry insights.
By actively participating in these networking opportunities, instrumentation engineers can build a robust professional network that supports their career growth and development.
Professional development and networking are essential for instrumentation engineers seeking to advance their careers. By engaging with professional organizations, attending conferences, pursuing continuing education, and actively networking, engineers can enhance their skills, stay updated on industry trends, and build valuable connections that can lead to new opportunities.
Key Takeaways
- Definition and Importance: Instrumentation engineering focuses on the design, development, and maintenance of instruments and systems that measure and control physical quantities. Its significance spans various industries, ensuring efficiency, safety, and compliance.
- Educational Pathways: A solid educational foundation is crucial, typically requiring a degree in engineering or a related field, along with specialized certifications and training programs to stay current with technological advancements.
- Core Responsibilities: Instrumentation engineers are responsible for designing systems, installing and calibrating instruments, troubleshooting issues, analyzing data, and ensuring adherence to safety standards.
- Essential Skills: Key competencies include technical skills in sensors and control systems, problem-solving abilities, and strong communication skills, all of which are vital for effective collaboration and project management.
- Tools and Technologies: Familiarity with software tools like MATLAB and LabVIEW, as well as hardware tools such as oscilloscopes, is essential. Emerging technologies like IoT and AI are increasingly shaping the field.
- Industry Applications: Instrumentation engineers find opportunities in diverse sectors, including oil and gas, manufacturing, pharmaceuticals, aerospace, and environmental monitoring, highlighting the versatility of the profession.
- Career Opportunities: The field offers a range of career paths from entry-level to specialized roles, with opportunities for freelance and consultancy work, making it a dynamic career choice.
- Future Trends: Staying informed about current challenges and future innovations is crucial for professionals in the field, as technological advancements continue to reshape instrumentation engineering.
- Professional Development: Engaging with professional organizations, attending conferences, and pursuing continuing education are vital for career growth and networking within the industry.
Conclusion
Instrumentation engineering is a critical field that combines technical expertise with innovative problem-solving to enhance operational efficiency across various industries. By understanding the core responsibilities, required skills, and emerging trends, aspiring engineers can effectively navigate their career paths and contribute to advancements in technology and safety. Continuous learning and professional networking are essential for success in this dynamic and evolving discipline.
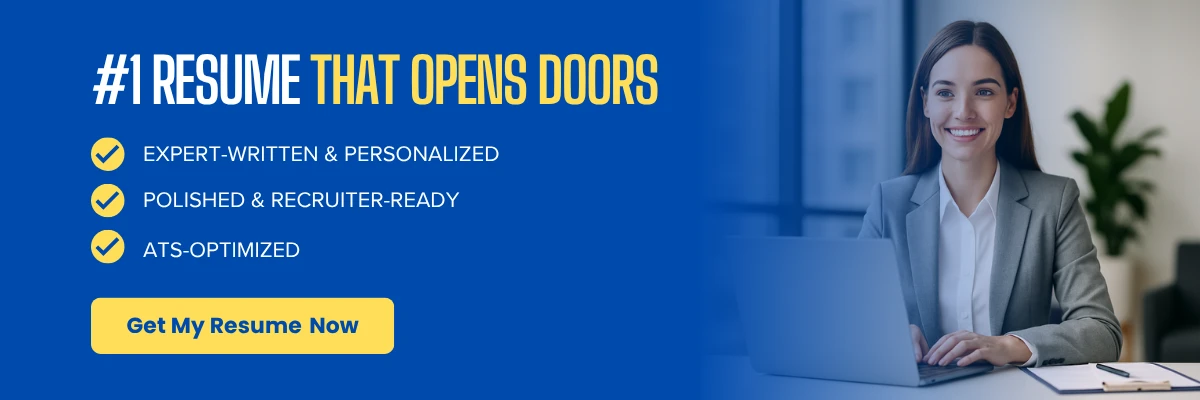
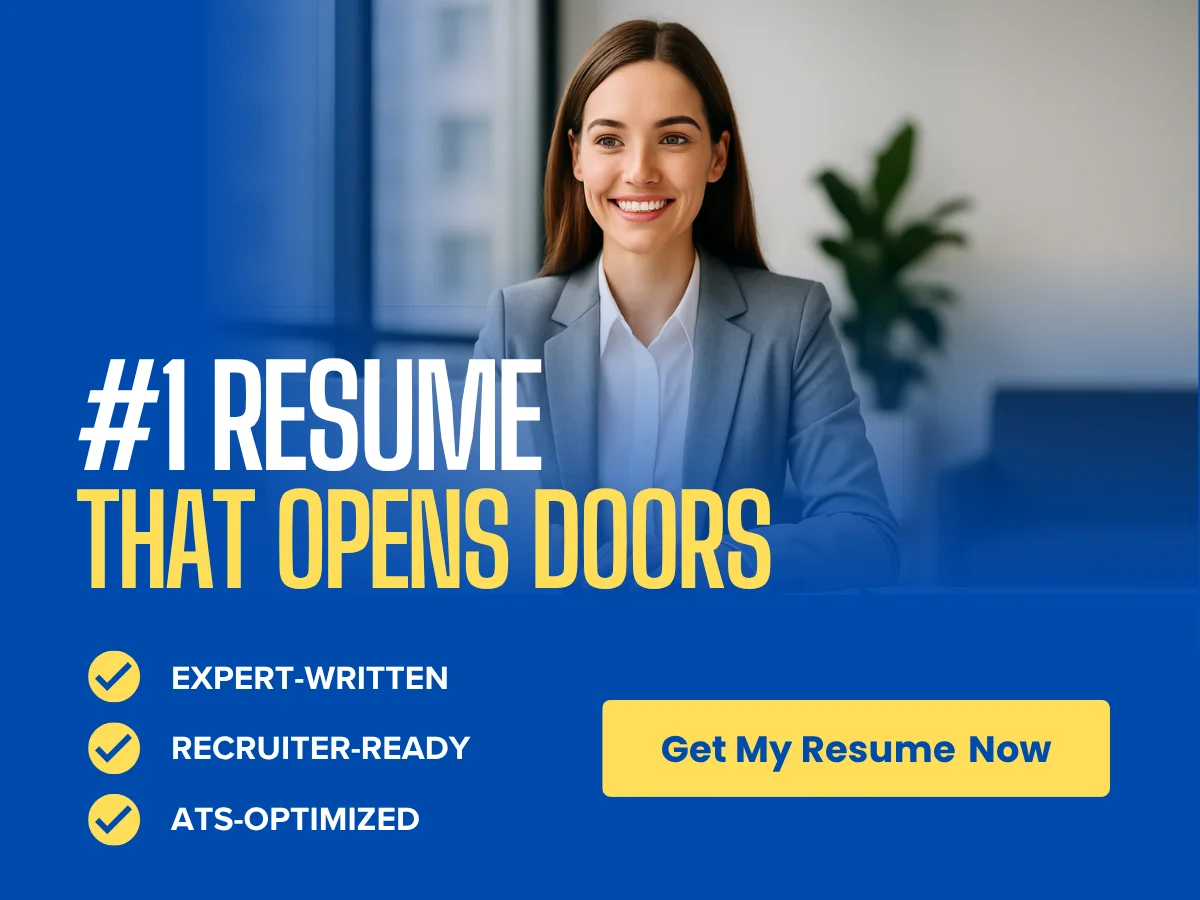