In the fast-paced world of manufacturing and production, the role of a Production Manager is pivotal to the success of any operation. These professionals are the backbone of production processes, ensuring that everything runs smoothly, efficiently, and on schedule. As industries evolve and technologies advance, the demand for skilled Production Managers has never been greater. But what exactly does it take to excel in this challenging role?
This essential guide delves into the top skills that every Production Manager should possess to thrive in today’s competitive landscape. From leadership and communication to problem-solving and technical expertise, we will explore the key competencies that not only enhance individual performance but also drive team success and organizational growth.
Whether you are an aspiring Production Manager looking to sharpen your skill set or an experienced professional seeking to stay ahead of industry trends, this article will provide valuable insights and practical tips. Join us as we uncover the essential skills that can elevate your career and contribute to the overall efficiency and effectiveness of your production team.
Technical Skills
In the fast-paced world of production management, technical skills are paramount. These skills not only enhance a production manager’s ability to oversee operations but also ensure that the production process runs smoothly, efficiently, and within budget. This section delves into the essential technical skills that every production manager should possess, including an exploration of production processes, proficiency in production software, knowledge of quality control standards, expertise in equipment and machinery, and an understanding of lean manufacturing techniques.
Exploring Production Processes
Understanding production processes is fundamental for any production manager. This encompasses a comprehensive knowledge of the entire production cycle, from raw material acquisition to the final product delivery. A production manager must be adept at mapping out these processes, identifying bottlenecks, and implementing solutions to enhance efficiency.
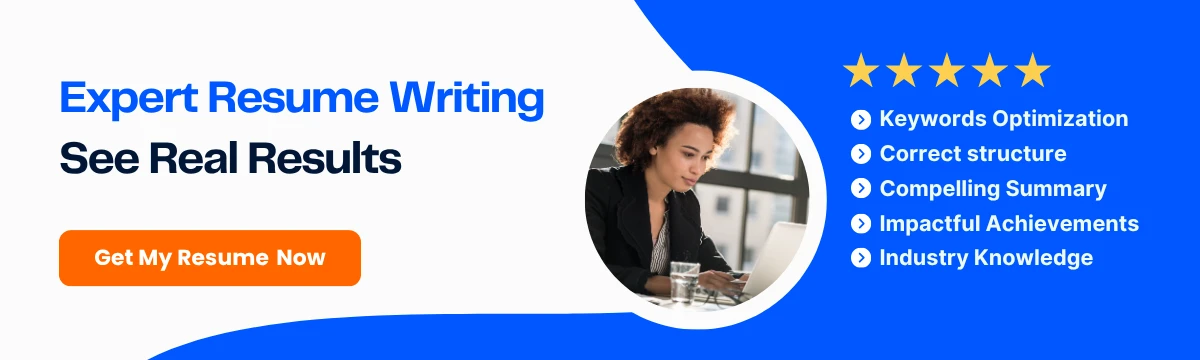
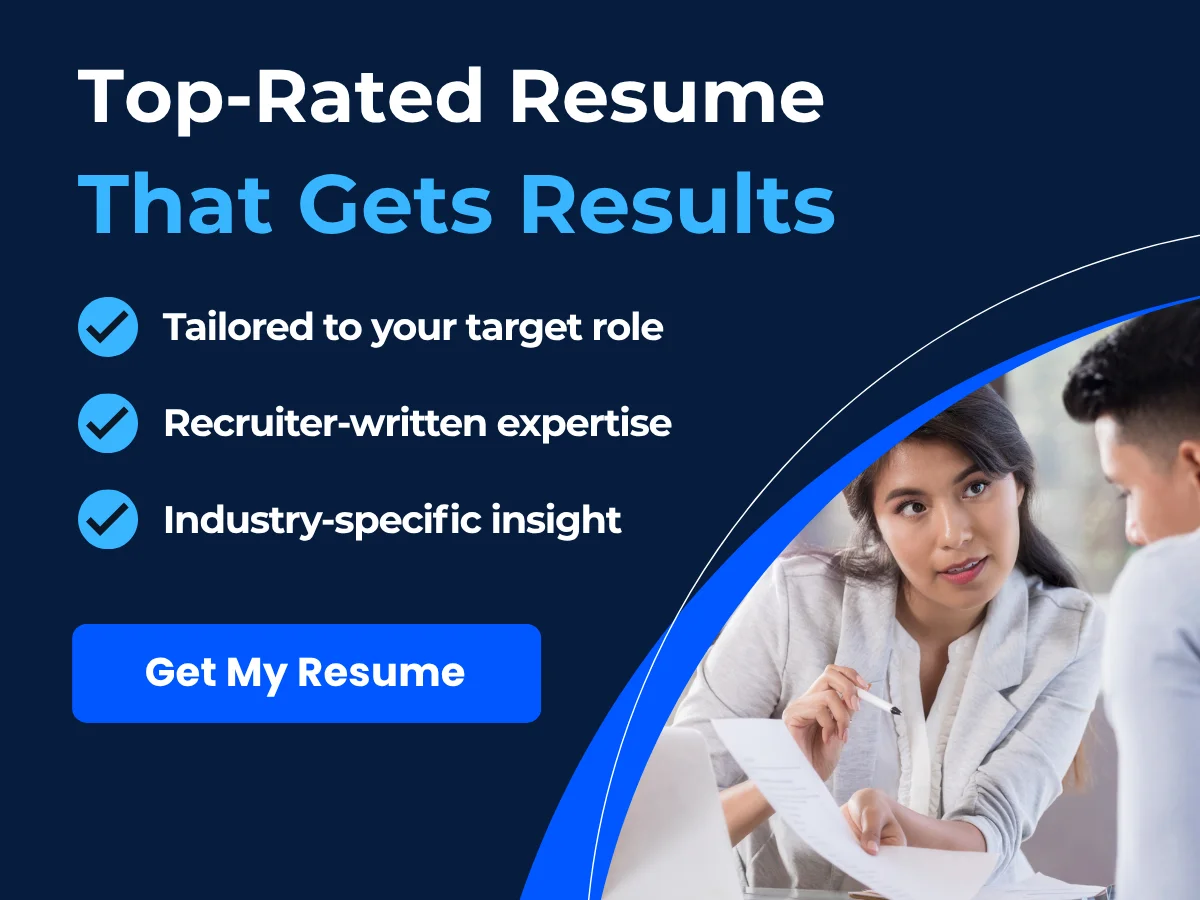
For instance, consider a manufacturing plant that produces automotive parts. A production manager must understand the various stages involved, such as:
- Material Procurement: Sourcing quality materials at the best prices.
- Production Planning: Scheduling production runs to meet demand while minimizing downtime.
- Assembly Line Management: Overseeing the workflow on the assembly line to ensure that each part is produced to specification.
- Logistics and Distribution: Coordinating the transportation of finished goods to customers.
By mastering these processes, production managers can optimize operations, reduce waste, and improve overall productivity. They can also leverage process mapping tools and methodologies, such as Value Stream Mapping (VSM), to visualize and analyze the flow of materials and information throughout the production cycle.
Proficiency in Production Software
In today’s digital age, proficiency in production software is a critical skill for production managers. Various software solutions are designed to streamline production processes, enhance communication, and provide real-time data analytics. Familiarity with these tools can significantly improve a manager’s ability to make informed decisions.
Some of the most commonly used production software includes:
- Enterprise Resource Planning (ERP) Systems: These systems integrate all facets of an operation, including planning, purchasing, inventory, sales, marketing, finance, and human resources. Popular ERP solutions like SAP and Oracle can help production managers track resources and optimize production schedules.
- Manufacturing Execution Systems (MES): MES software provides real-time data on production processes, allowing managers to monitor performance, track work-in-progress, and ensure compliance with quality standards. Examples include Siemens Opcenter and Rockwell Automation’s FactoryTalk.
- Project Management Tools: Tools like Trello, Asana, or Microsoft Project can help production managers plan, execute, and monitor production projects, ensuring that timelines and budgets are adhered to.
By leveraging these software solutions, production managers can enhance their operational efficiency, improve communication across departments, and make data-driven decisions that positively impact production outcomes.
Knowledge of Quality Control Standards
Quality control is a critical aspect of production management. A production manager must have a thorough understanding of quality control standards to ensure that products meet both internal and external quality requirements. This includes knowledge of industry-specific standards, such as ISO 9001, Six Sigma, and Total Quality Management (TQM).
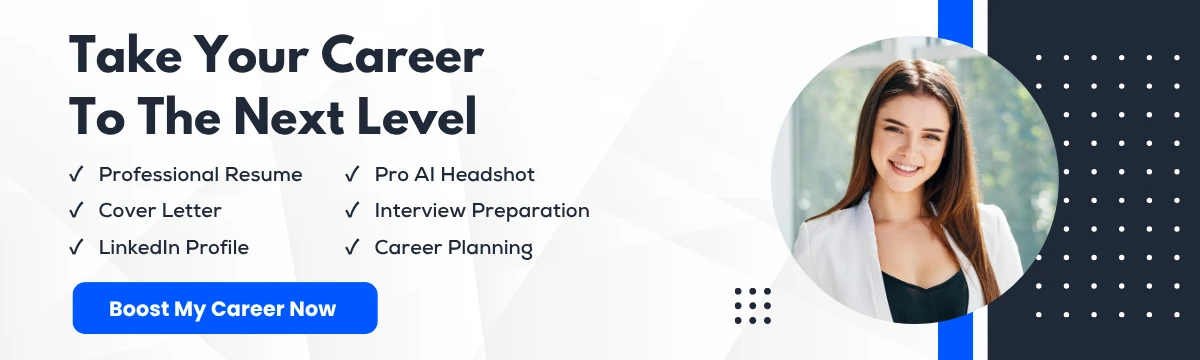
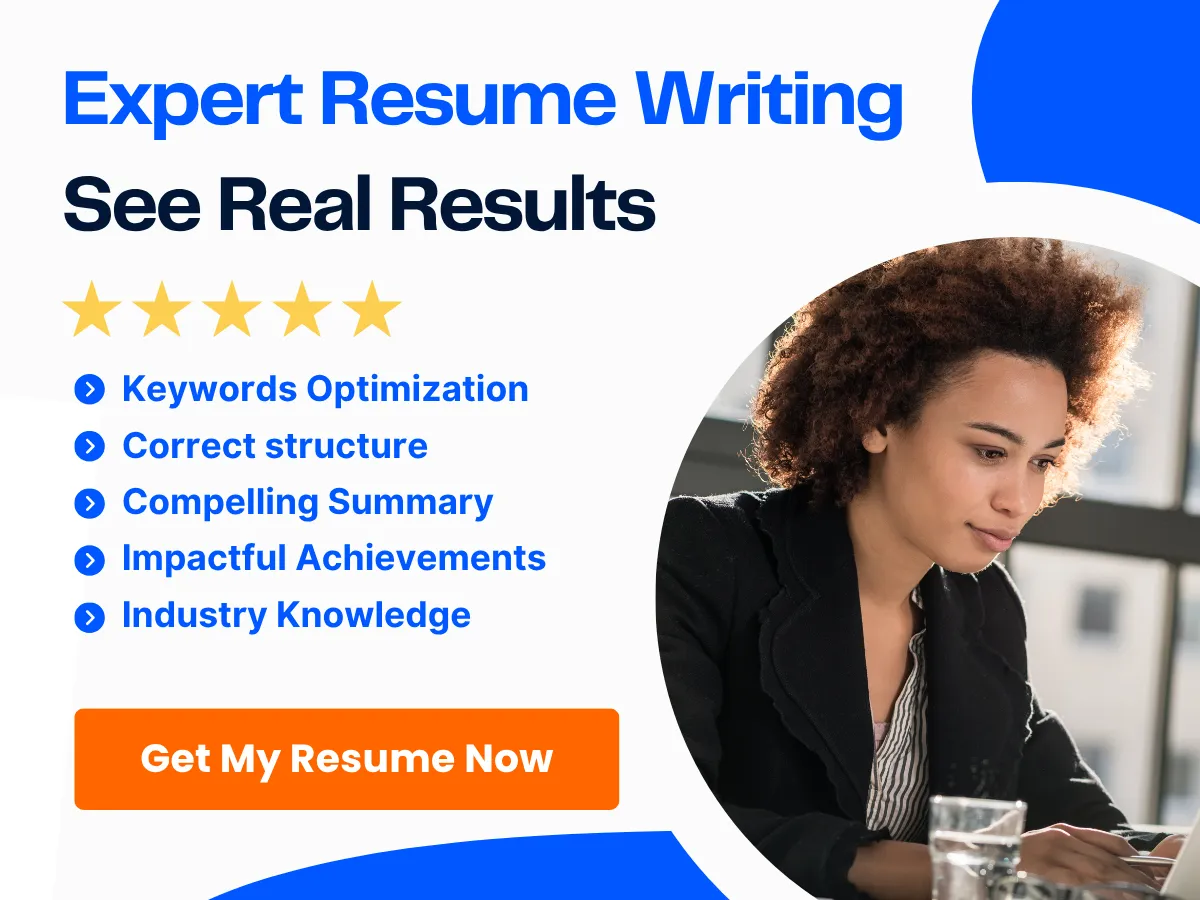
For example, a production manager in the food industry must be familiar with Hazard Analysis Critical Control Point (HACCP) principles to ensure food safety and compliance with regulations. Similarly, in the electronics manufacturing sector, adherence to IPC standards is crucial for maintaining product quality.
Implementing a robust quality control system involves:
- Defining Quality Metrics: Establishing clear quality metrics that align with customer expectations and regulatory requirements.
- Conducting Regular Inspections: Performing routine inspections and audits to identify defects and areas for improvement.
- Training Staff: Ensuring that all employees are trained in quality control procedures and understand their role in maintaining product quality.
- Utilizing Statistical Process Control (SPC): Applying SPC techniques to monitor and control production processes, helping to identify variations and implement corrective actions.
By prioritizing quality control, production managers can reduce defects, enhance customer satisfaction, and ultimately drive business success.
Equipment and Machinery Expertise
A production manager must possess a solid understanding of the equipment and machinery used in the production process. This includes knowledge of how to operate, maintain, and troubleshoot various types of machinery, as well as an understanding of the latest technological advancements in the field.
For instance, in a manufacturing facility, a production manager should be familiar with:
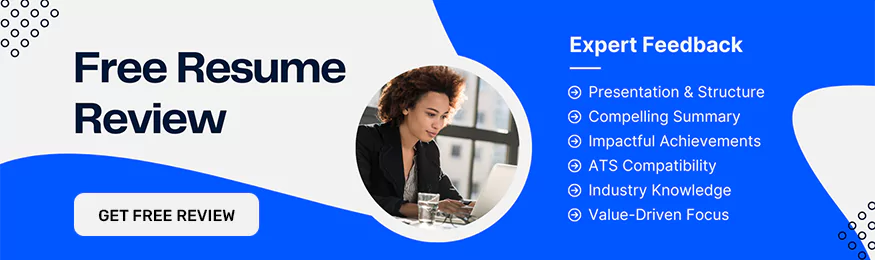
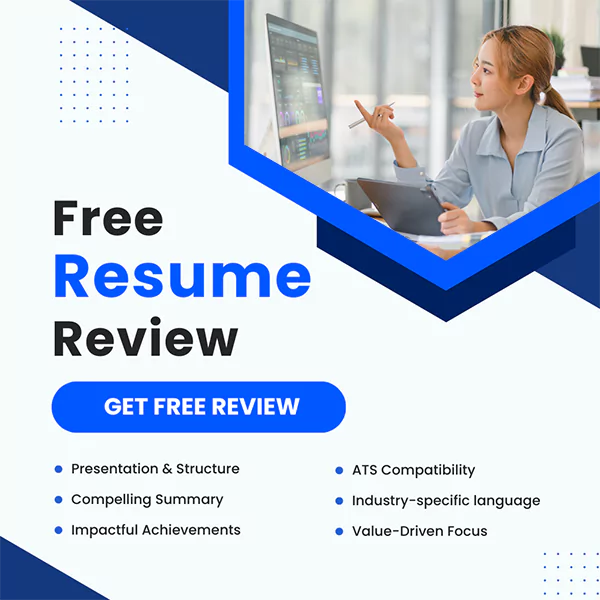
- Machinery Operation: Understanding how to operate machinery safely and efficiently, including CNC machines, lathes, and assembly robots.
- Preventive Maintenance: Implementing a preventive maintenance program to minimize downtime and extend the lifespan of equipment.
- Safety Standards: Ensuring compliance with safety regulations and standards, such as OSHA guidelines, to protect employees and reduce the risk of accidents.
Moreover, staying updated on emerging technologies, such as automation and Industry 4.0 innovations, can provide a competitive edge. For example, a production manager who understands the benefits of integrating IoT devices into machinery can enhance data collection and improve decision-making processes.
Lean Manufacturing Techniques
Lean manufacturing is a philosophy that focuses on minimizing waste while maximizing productivity. A production manager should be well-versed in lean principles and techniques to create a more efficient production environment. This involves identifying and eliminating non-value-added activities, streamlining processes, and fostering a culture of continuous improvement.
Key lean manufacturing techniques include:
- 5S Methodology: A workplace organization method that promotes efficiency and effectiveness through five steps: Sort, Set in order, Shine, Standardize, and Sustain.
- Kaizen: A continuous improvement strategy that encourages all employees to contribute ideas for enhancing processes and reducing waste.
- Just-In-Time (JIT) Production: A strategy that aims to reduce inventory costs by producing only what is needed, when it is needed.
- Value Stream Mapping: A visual tool used to analyze the flow of materials and information, helping to identify areas for improvement.
By implementing lean manufacturing techniques, production managers can significantly enhance operational efficiency, reduce costs, and improve product quality. This not only benefits the organization but also contributes to a more sustainable production model.
Technical skills are the backbone of effective production management. By mastering production processes, software tools, quality control standards, equipment expertise, and lean manufacturing techniques, production managers can drive their organizations toward greater efficiency and success.
Leadership and Management Skills
In the fast-paced world of production management, leadership and management skills are not just beneficial; they are essential. A production manager is responsible for overseeing the entire production process, ensuring that operations run smoothly, efficiently, and within budget. This section delves into the critical leadership and management skills that every production manager should cultivate to excel in their role.
Team Leadership and Motivation
Effective team leadership is at the heart of successful production management. A production manager must inspire and motivate their team to achieve high levels of performance. This involves understanding individual team members’ strengths and weaknesses and leveraging them to create a cohesive unit.

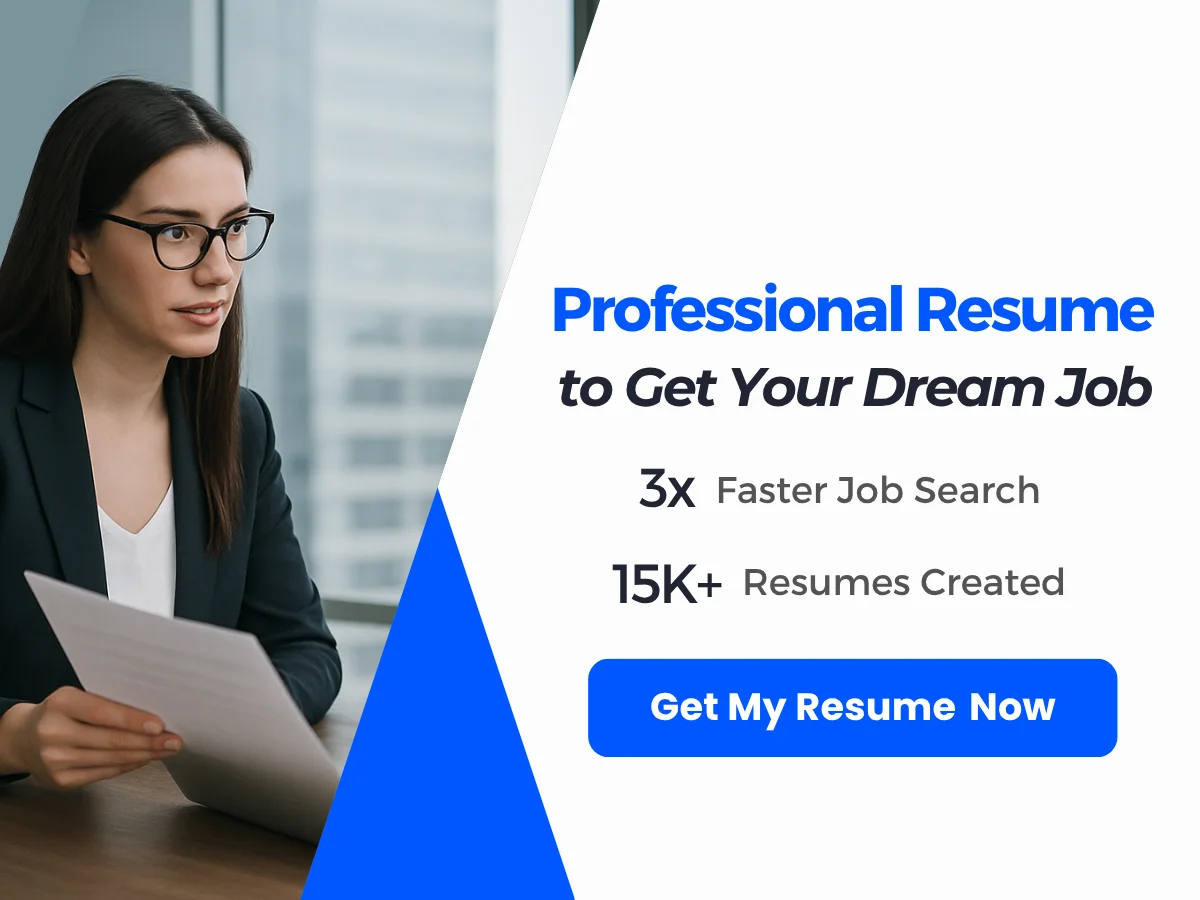
One effective strategy for team leadership is to establish clear goals and expectations. By setting specific, measurable, achievable, relevant, and time-bound (SMART) goals, production managers can provide their teams with a clear direction. For example, if a production line is expected to increase output by 20% over the next quarter, the manager should communicate this goal clearly and outline the steps necessary to achieve it.
Moreover, recognizing and rewarding team members for their contributions can significantly boost morale and motivation. This could be as simple as verbal recognition during team meetings or more formal rewards such as bonuses or employee of the month programs. A motivated team is more likely to be productive and engaged, leading to better overall performance.
Conflict Resolution and Negotiation
In any workplace, conflicts are inevitable. Production managers must be equipped with conflict resolution and negotiation skills to address issues promptly and effectively. Conflicts can arise from various sources, including differences in opinion, resource allocation, or interpersonal relationships among team members.
To resolve conflicts, production managers should first approach the situation with an open mind. Listening to all parties involved is crucial to understanding the root cause of the conflict. For instance, if two team members disagree on the best approach to a production issue, the manager should facilitate a discussion where both can express their viewpoints. This not only helps in finding a resolution but also fosters a culture of open communication.
Negotiation skills are equally important, especially when dealing with suppliers, clients, or other departments within the organization. A production manager may need to negotiate for better pricing on materials or for additional resources to meet production demands. Effective negotiation involves understanding the needs and constraints of all parties and finding a mutually beneficial solution. For example, a production manager might negotiate a bulk purchase discount with a supplier while agreeing to a longer payment term, benefiting both parties.
Performance Management
Performance management is a critical aspect of a production manager’s role. It involves setting performance standards, monitoring progress, and providing feedback to team members. A production manager must be adept at using various performance metrics to assess the efficiency and effectiveness of the production process.
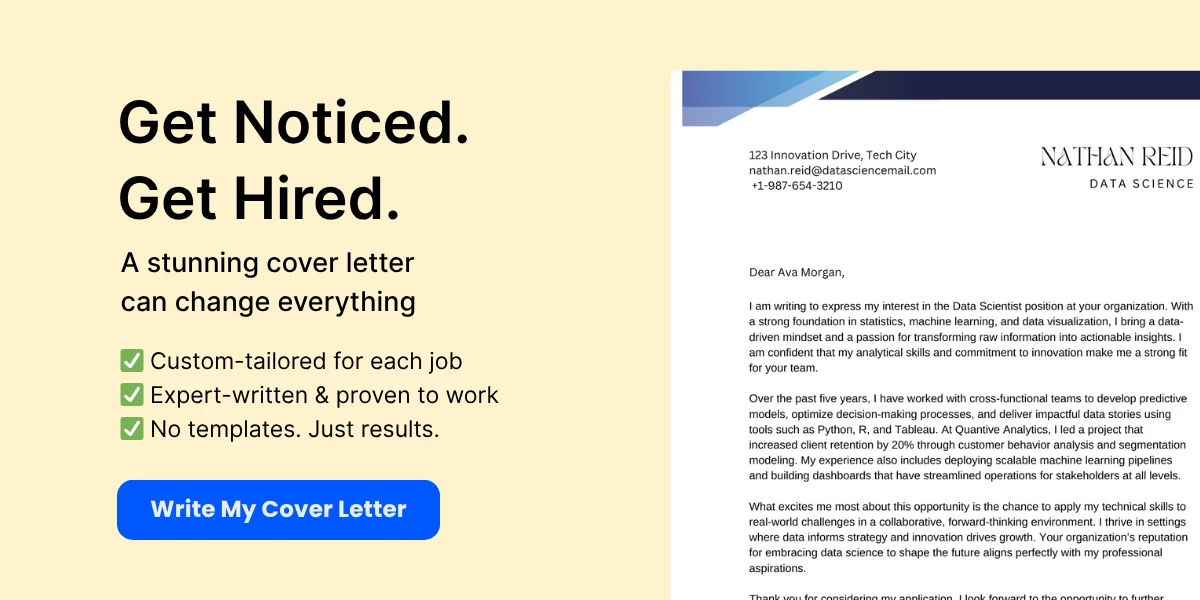
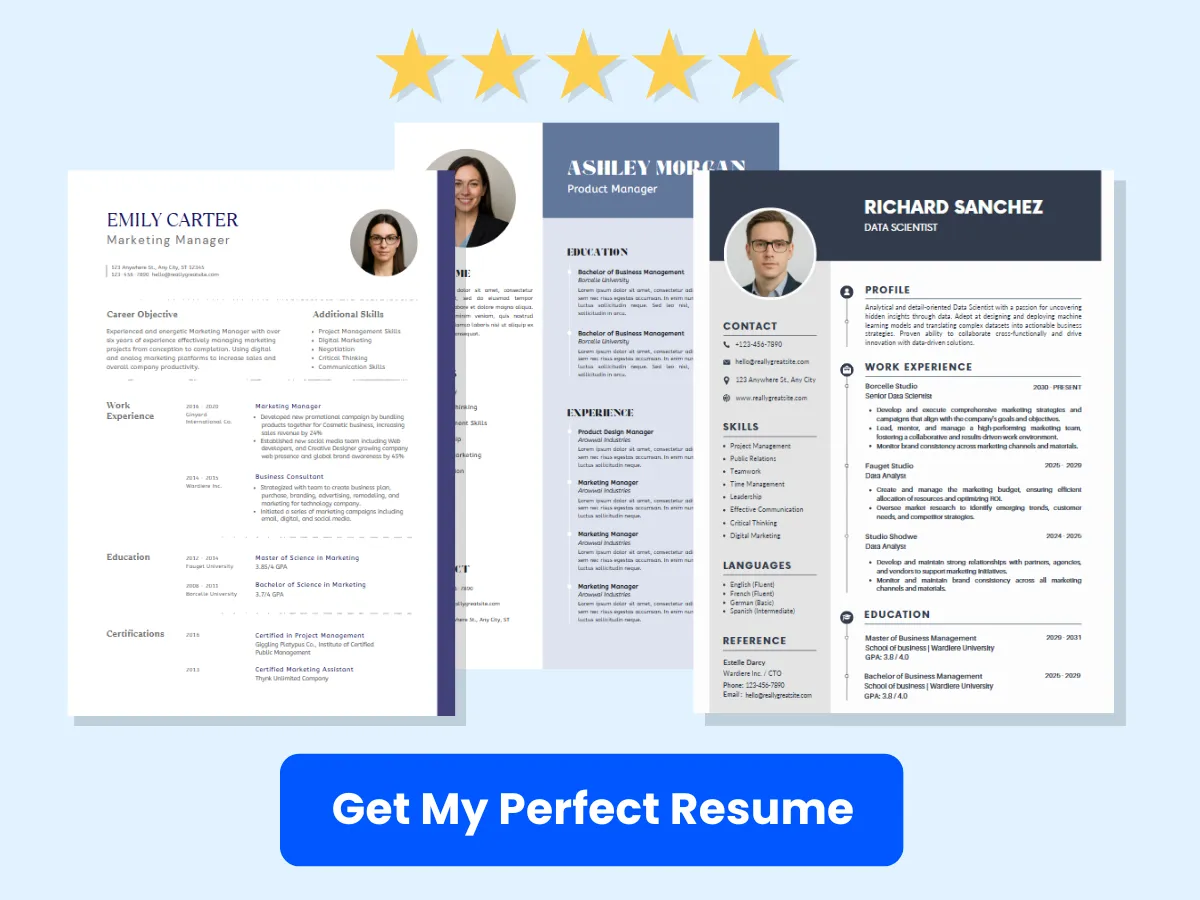
Key performance indicators (KPIs) such as production output, quality control metrics, and downtime statistics are essential for evaluating performance. For instance, if a production line is consistently falling short of its output targets, the manager must analyze the data to identify the underlying issues. This could involve examining machine performance, employee productivity, or workflow processes.
Regular performance reviews are also vital. These reviews provide an opportunity for managers to discuss performance with team members, set new goals, and address any areas for improvement. Constructive feedback is essential; it should be specific, actionable, and focused on behaviors rather than personal attributes. For example, instead of saying, “You are not a good worker,” a manager might say, “I noticed that the last batch had several defects. Let’s discuss how we can improve quality control moving forward.”
Delegation and Task Management
Effective delegation is a hallmark of strong leadership. A production manager must be able to delegate tasks appropriately to ensure that the workload is balanced and that team members are empowered to take ownership of their responsibilities. Delegation not only helps in managing time and resources but also fosters skill development among team members.
When delegating tasks, it is essential to match the right person with the right task. For example, if a team member excels in quality control, assigning them to oversee quality checks during production can enhance efficiency and accuracy. Additionally, providing clear instructions and expectations when delegating tasks is crucial. This ensures that team members understand their responsibilities and the desired outcomes.
Task management tools can also aid in effective delegation. Utilizing project management software can help production managers track progress, set deadlines, and communicate with team members. This transparency allows everyone to stay informed about their responsibilities and deadlines, reducing the likelihood of misunderstandings or missed tasks.
Change Management
In the dynamic environment of production, change is a constant. Whether it’s implementing new technologies, adjusting production processes, or responding to market demands, production managers must be adept at change management. This involves not only managing the technical aspects of change but also addressing the human side of it.
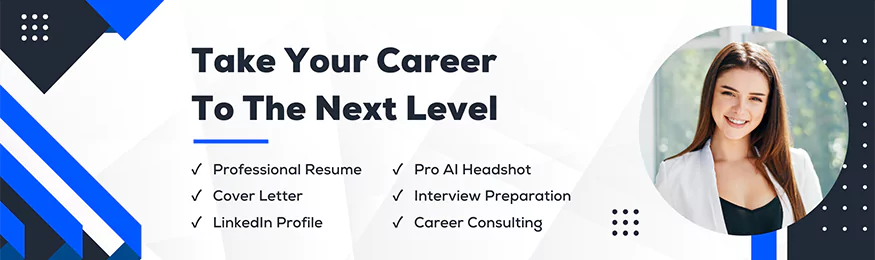
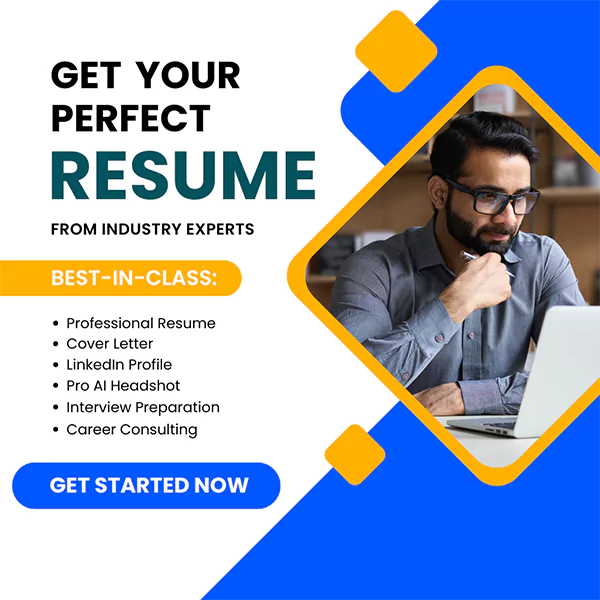
Successful change management begins with clear communication. Production managers should articulate the reasons for the change, the benefits it will bring, and how it will impact the team. For instance, if a new production line is being introduced, the manager should explain how this will improve efficiency and potentially lead to job growth within the company.
Involving team members in the change process can also facilitate smoother transitions. By seeking input and feedback from the team, managers can identify potential challenges and address them proactively. This collaborative approach fosters a sense of ownership and reduces resistance to change.
Training and support are also critical components of change management. Providing team members with the necessary training to adapt to new processes or technologies ensures that they feel confident and competent in their roles. For example, if a new software system is being implemented, offering training sessions can help team members transition smoothly and maintain productivity.
Leadership and management skills are fundamental to the success of production managers. By honing skills in team leadership and motivation, conflict resolution and negotiation, performance management, delegation and task management, and change management, production managers can lead their teams effectively and drive operational excellence.
Communication Skills
In the fast-paced world of production management, effective communication is not just a skill; it is a cornerstone of successful operations. Production managers are the linchpins that connect various departments, ensuring that everyone is aligned with the production goals and timelines. This section delves into the essential communication skills that every production manager should master, including effective verbal communication, written communication proficiency, active listening, cross-departmental collaboration, and public speaking and presentation skills.
Effective Verbal Communication
Verbal communication is the most immediate form of interaction and is crucial for production managers who need to convey instructions, provide feedback, and motivate their teams. Effective verbal communication involves clarity, conciseness, and the ability to adapt your message to your audience.
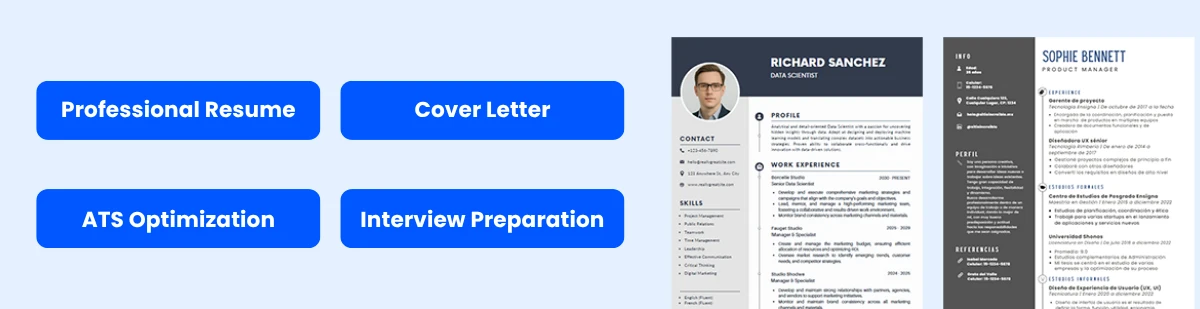
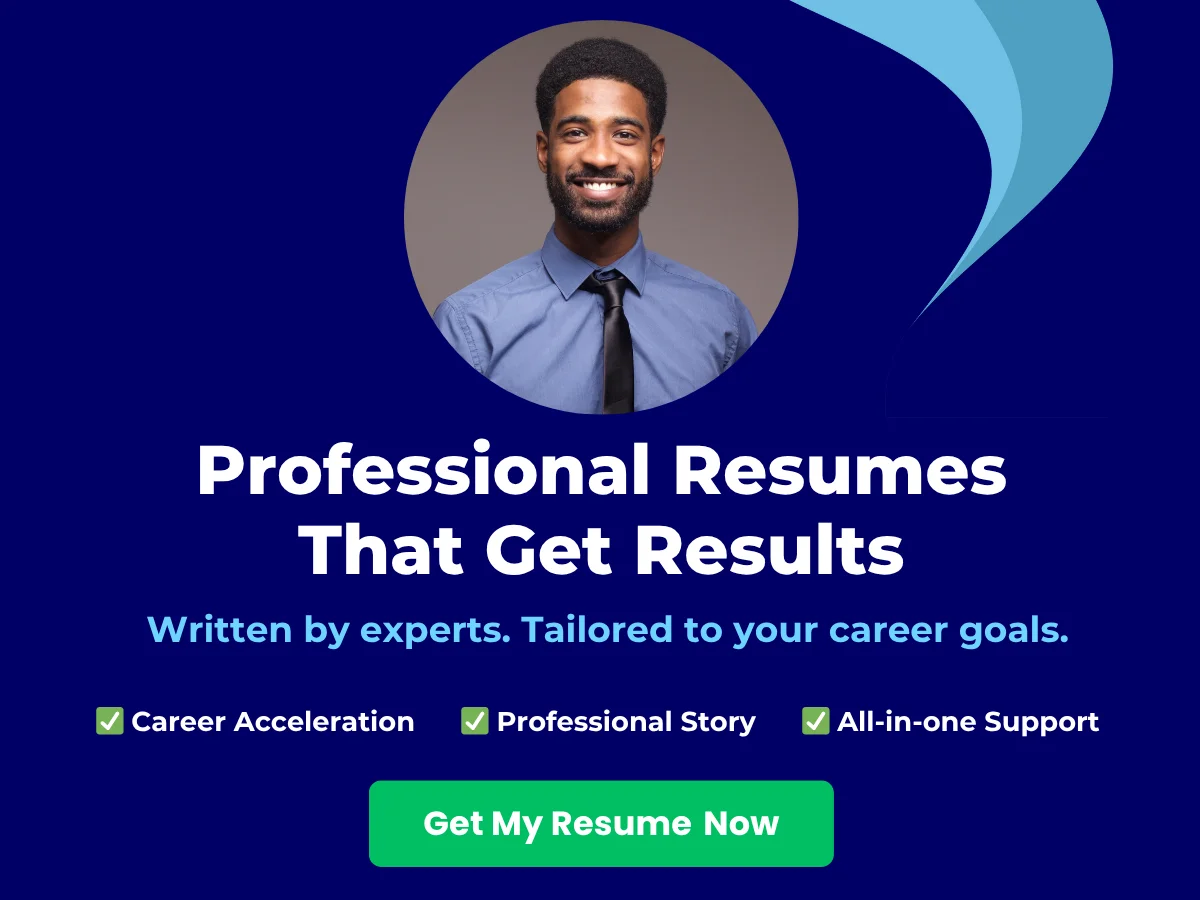
For instance, when addressing a team of engineers, a production manager might use technical jargon that resonates with their expertise. Conversely, when communicating with non-technical staff, simplifying complex concepts is essential. This adaptability not only fosters understanding but also builds trust and rapport among team members.
Moreover, tone and body language play significant roles in verbal communication. A confident tone can inspire confidence in your team, while positive body language—such as maintaining eye contact and using open gestures—can enhance the message being delivered. Regular team meetings, one-on-one check-ins, and informal conversations are all opportunities for production managers to practice and refine their verbal communication skills.
Written Communication Proficiency
In an age where digital communication is prevalent, written communication proficiency is indispensable for production managers. This skill encompasses the ability to write clear emails, reports, and documentation that convey information effectively and efficiently.
For example, a production manager may need to draft a production schedule or a project update report. These documents must be well-structured, free of jargon, and easy to understand. Utilizing bullet points, headings, and concise paragraphs can enhance readability. Additionally, being proficient in various communication tools—such as project management software, email platforms, and collaborative tools like Slack or Microsoft Teams—can streamline communication processes.
Furthermore, written communication is not just about clarity; it also involves professionalism. A well-crafted email can set the tone for a project, while poorly written communication can lead to misunderstandings and decreased morale. Therefore, production managers should invest time in honing their writing skills, perhaps through workshops or online courses, to ensure their written communication is as effective as their verbal interactions.
Active Listening
Active listening is a critical component of effective communication that is often overlooked. It involves fully concentrating, understanding, responding, and remembering what is being said. For production managers, active listening is vital for gathering feedback, understanding team dynamics, and resolving conflicts.
When a team member approaches a production manager with a concern or suggestion, practicing active listening means giving them your full attention, acknowledging their feelings, and responding thoughtfully. This not only validates the speaker but also encourages open dialogue, fostering a culture of trust and collaboration.
For instance, during a production meeting, a team member might express frustration over a bottleneck in the workflow. By actively listening—nodding, maintaining eye contact, and paraphrasing their concerns—the production manager can better understand the issue and work collaboratively to find a solution. This approach not only resolves the immediate problem but also empowers team members, making them feel valued and heard.
Cross-Departmental Collaboration
Production managers often serve as the bridge between various departments, including engineering, quality assurance, supply chain, and sales. Effective cross-departmental collaboration is essential for ensuring that production goals align with overall business objectives.
To facilitate collaboration, production managers must possess strong interpersonal skills and the ability to communicate effectively across different teams. This may involve organizing joint meetings, creating cross-functional teams for specific projects, or using collaborative tools that allow for real-time communication and updates.
For example, if a production manager is launching a new product, they must coordinate with the marketing team to ensure that production timelines align with promotional campaigns. By fostering open lines of communication and encouraging feedback from all departments, production managers can create a more cohesive work environment that enhances productivity and innovation.
Additionally, understanding the unique challenges and goals of each department can help production managers tailor their communication strategies. For instance, while the engineering team may prioritize technical specifications, the sales team may focus on customer feedback and market trends. By recognizing these differences, production managers can facilitate more effective discussions and drive better outcomes.
Public Speaking and Presentation
Public speaking and presentation skills are essential for production managers who need to communicate with larger audiences, such as stakeholders, upper management, or external partners. Whether presenting a project update, leading a training session, or pitching a new initiative, the ability to engage and inform an audience is crucial.
To excel in public speaking, production managers should focus on several key areas:
- Preparation: Thoroughly prepare your material, ensuring that it is relevant and tailored to your audience. Use visual aids, such as slides or charts, to enhance understanding.
- Practice: Rehearse your presentation multiple times to build confidence and refine your delivery. Consider recording yourself to identify areas for improvement.
- Engagement: Engage your audience by asking questions, encouraging participation, and using storytelling techniques to make your message more relatable.
- Feedback: After your presentation, seek feedback from peers or mentors to identify strengths and areas for growth.
For instance, a production manager may need to present quarterly production results to the executive team. By preparing a clear and concise presentation that highlights key metrics, challenges, and proposed solutions, they can effectively communicate the state of production and garner support for necessary changes.
Communication skills are paramount for production managers. Mastering effective verbal and written communication, practicing active listening, fostering cross-departmental collaboration, and honing public speaking abilities are all essential components that contribute to a production manager’s success. By investing in these skills, production managers can enhance their leadership capabilities, drive team performance, and ultimately contribute to the overall success of their organization.
Problem-Solving and Decision-Making Skills
In the fast-paced world of production management, the ability to solve problems and make informed decisions is paramount. Production managers are often faced with unexpected challenges that require quick thinking and effective strategies. This section delves into the essential problem-solving and decision-making skills that every production manager should cultivate, including analytical thinking, root cause analysis, strategic planning, risk assessment and management, and crisis management.
Analytical Thinking
Analytical thinking is the ability to break down complex problems into manageable parts, allowing for a clearer understanding of the situation at hand. For production managers, this skill is crucial when evaluating production processes, identifying inefficiencies, and implementing improvements.
For instance, consider a scenario where a production line is experiencing delays. An analytical thinker would first gather data on the production process, such as cycle times, machine performance, and workforce efficiency. By analyzing this data, they can identify patterns or bottlenecks that may be causing the delays. This methodical approach not only helps in diagnosing the problem but also aids in developing targeted solutions.
Moreover, analytical thinking extends beyond just identifying problems. It also involves forecasting potential outcomes based on current data. For example, a production manager might analyze historical production data to predict future output levels, enabling better resource allocation and scheduling.
Root Cause Analysis
Root cause analysis (RCA) is a systematic approach used to identify the underlying causes of problems rather than just addressing their symptoms. This skill is vital for production managers who need to ensure that issues are resolved effectively and do not recur.
One common method of conducting RCA is the “5 Whys” technique, where a manager asks “why” multiple times (typically five) to drill down to the root cause of a problem. For example, if a machine breaks down, the first “why” might be, “Why did the machine break down?” The answer could be “because it was not maintained properly.” The next “why” would then explore why maintenance was neglected, and so on, until the fundamental issue is uncovered.
By employing root cause analysis, production managers can implement long-term solutions that enhance operational efficiency. For instance, if the root cause of frequent machine breakdowns is identified as a lack of scheduled maintenance, the manager can establish a regular maintenance program, thereby reducing downtime and improving productivity.
Strategic Planning
Strategic planning involves setting long-term goals and determining the best course of action to achieve them. For production managers, this skill is essential for aligning production capabilities with the overall business objectives of the organization.
Effective strategic planning requires a deep understanding of both the internal and external environments. Internally, production managers must assess their resources, capabilities, and workforce. Externally, they need to consider market trends, customer demands, and competitive pressures. By synthesizing this information, production managers can develop a strategic plan that not only meets production targets but also supports the company’s growth and sustainability.
For example, a production manager might identify a growing demand for eco-friendly products. In response, they could develop a strategic plan to transition the production line to incorporate sustainable materials and processes. This not only positions the company favorably in the market but also aligns with broader environmental goals.
Risk Assessment and Management
Risk assessment and management are critical skills for production managers, as they must navigate various uncertainties that can impact production efficiency and safety. This involves identifying potential risks, evaluating their likelihood and impact, and developing strategies to mitigate them.
For instance, a production manager might conduct a risk assessment to evaluate the potential impact of supply chain disruptions. By analyzing factors such as supplier reliability, geopolitical issues, and natural disasters, they can develop contingency plans to ensure production continuity. This might include diversifying suppliers or maintaining safety stock of critical materials.
Moreover, risk management is not just about avoiding negative outcomes; it also involves seizing opportunities. For example, a production manager might identify a risk in the form of a new competitor entering the market. By assessing this risk, they can develop strategies to enhance their product offerings or improve customer service, turning a potential threat into a competitive advantage.
Crisis Management
Crisis management is the ability to respond effectively to unexpected events that threaten the stability of production operations. This skill is particularly important for production managers, as crises can arise from various sources, including equipment failures, supply chain disruptions, or even public relations issues.
Effective crisis management begins with preparation. Production managers should develop crisis management plans that outline procedures for various scenarios. This includes establishing communication protocols, assigning roles and responsibilities, and conducting regular training exercises to ensure that the team is ready to respond swiftly and effectively.
For example, if a critical piece of machinery fails, a well-prepared production manager would have a plan in place to quickly assess the situation, communicate with the team, and implement backup procedures to minimize downtime. This might involve reallocating resources, adjusting production schedules, or even bringing in temporary equipment to keep operations running smoothly.
Additionally, after a crisis has been managed, it is essential to conduct a thorough review to identify lessons learned. This reflection can lead to improvements in processes and crisis management plans, ultimately strengthening the organization’s resilience against future challenges.
Problem-solving and decision-making skills are indispensable for production managers. By honing their analytical thinking, mastering root cause analysis, engaging in strategic planning, conducting risk assessments, and developing crisis management strategies, production managers can navigate the complexities of their roles and drive their organizations toward success.
Time Management and Organizational Skills
In the fast-paced world of production management, time management and organizational skills are not just beneficial; they are essential. Production managers are responsible for overseeing the entire production process, ensuring that projects are completed on time, within budget, and to the required quality standards. This section delves into the key components of effective time management and organizational skills, providing insights and techniques that can help production managers excel in their roles.
Prioritization Techniques
Effective prioritization is the cornerstone of successful time management. Production managers often juggle multiple tasks and projects simultaneously, making it crucial to identify which tasks require immediate attention and which can be scheduled for later. Here are some popular prioritization techniques:
- The Eisenhower Matrix: This method categorizes tasks into four quadrants based on urgency and importance. Tasks that are both urgent and important should be tackled first, while those that are neither can be delegated or eliminated.
- ABC Method: In this technique, tasks are classified into three categories: A (high priority), B (medium priority), and C (low priority). This helps production managers focus on what truly matters and allocate resources accordingly.
- MoSCoW Method: This approach divides tasks into four categories: Must have, Should have, Could have, and Won’t have. This method is particularly useful in project management, allowing production managers to align their team’s efforts with project goals.
By employing these prioritization techniques, production managers can ensure that they are focusing their efforts on the most critical tasks, thereby enhancing productivity and efficiency.
Scheduling and Planning
Scheduling and planning are integral to the success of any production operation. A well-structured schedule not only helps in tracking progress but also ensures that resources are allocated effectively. Here are some strategies for effective scheduling and planning:
- Gantt Charts: These visual tools provide a timeline for project tasks, allowing production managers to see the start and end dates of each task, as well as their dependencies. Gantt charts facilitate better communication among team members and stakeholders.
- Kanban Boards: This method uses visual signals to represent work items and their progress. Kanban boards help production managers visualize workflow, identify bottlenecks, and optimize resource allocation.
- Time Blocking: This technique involves allocating specific blocks of time for different tasks or activities. By dedicating uninterrupted time to critical tasks, production managers can enhance focus and productivity.
Effective scheduling and planning not only streamline operations but also help in anticipating potential challenges, allowing production managers to proactively address issues before they escalate.
Workflow Optimization
Workflow optimization is about making processes more efficient and effective. Production managers must continuously assess and refine workflows to eliminate waste, reduce delays, and enhance productivity. Here are some strategies for optimizing workflows:
- Process Mapping: This involves creating a visual representation of the workflow, highlighting each step in the process. By mapping out workflows, production managers can identify redundancies and areas for improvement.
- Lean Manufacturing Principles: Adopting lean principles can help production managers minimize waste and maximize value. Techniques such as 5S (Sort, Set in order, Shine, Standardize, Sustain) can lead to more organized and efficient workspaces.
- Continuous Improvement (Kaizen): This philosophy encourages ongoing, incremental improvements in processes. By fostering a culture of continuous improvement, production managers can empower their teams to identify and implement enhancements.
By focusing on workflow optimization, production managers can create a more agile and responsive production environment, ultimately leading to better outcomes.
Multitasking Abilities
In the realm of production management, multitasking is often a necessary skill. Production managers frequently find themselves handling various responsibilities simultaneously, from coordinating with suppliers to managing team dynamics. However, effective multitasking requires more than just juggling tasks; it involves strategic thinking and prioritization. Here are some tips for enhancing multitasking abilities:
- Set Clear Goals: Establishing clear, achievable goals for each task can help production managers stay focused and organized, even when managing multiple responsibilities.
- Use Technology: Leveraging project management software and tools can streamline communication and task management, making it easier to track progress across multiple projects.
- Delegate Wisely: Recognizing when to delegate tasks is crucial for effective multitasking. Production managers should empower their team members to take ownership of specific tasks, allowing them to focus on higher-level responsibilities.
While multitasking can enhance productivity, it is essential for production managers to remain mindful of their limits. Overcommitting can lead to burnout and decreased efficiency, so finding a balance is key.
Deadline Management
Meeting deadlines is a critical aspect of production management. Delays can have significant repercussions, including increased costs, dissatisfied clients, and damaged reputations. Therefore, effective deadline management is paramount. Here are some strategies to ensure deadlines are met:
- Set Realistic Deadlines: When planning projects, production managers should consider the complexity of tasks and the availability of resources. Setting achievable deadlines helps prevent last-minute rushes and ensures quality outcomes.
- Regular Check-Ins: Frequent progress updates and check-ins with team members can help identify potential delays early on. This proactive approach allows production managers to address issues before they impact the overall timeline.
- Buffer Time: Incorporating buffer time into project schedules can provide a safety net for unforeseen delays. This extra time can be crucial in maintaining project timelines and ensuring that deadlines are met.
By mastering deadline management, production managers can foster a culture of accountability and reliability within their teams, ultimately leading to successful project completions.
Time management and organizational skills are vital for production managers. By mastering prioritization techniques, effective scheduling and planning, workflow optimization, multitasking abilities, and deadline management, production managers can enhance their effectiveness and drive their teams toward success. These skills not only contribute to individual performance but also play a significant role in the overall success of production operations.
Financial Acumen
In the fast-paced world of production management, financial acumen is not just a desirable skill; it is essential. Production managers are often tasked with overseeing budgets, controlling costs, and ensuring that resources are allocated efficiently. This section delves into the critical components of financial acumen that every production manager should master, including budgeting and cost control, financial reporting and analysis, resource allocation, ROI and cost-benefit analysis, and vendor and supplier management.
Budgeting and Cost Control
Budgeting is the backbone of financial management in any production environment. A well-structured budget allows production managers to plan for the future, allocate resources effectively, and monitor financial performance. The budgeting process typically involves estimating revenues and expenses over a specific period, often a fiscal year.
To create an effective budget, production managers should:
- Analyze Historical Data: Review past financial performance to identify trends and make informed predictions about future costs and revenues.
- Engage Stakeholders: Collaborate with team members from various departments to gather insights and ensure that the budget reflects the needs of the entire organization.
- Set Realistic Goals: Establish achievable financial targets that align with the company’s overall objectives.
- Monitor and Adjust: Regularly review budget performance and make adjustments as necessary to respond to changing conditions.
Cost control is equally important. It involves monitoring expenses to ensure they remain within the budget. Production managers can implement cost control measures by:
- Tracking Expenses: Use software tools to track spending in real-time, allowing for immediate identification of variances from the budget.
- Implementing Efficiency Measures: Identify areas where processes can be streamlined to reduce costs without sacrificing quality.
- Conducting Regular Audits: Perform periodic audits to ensure compliance with budgetary constraints and identify potential areas for cost savings.
Financial Reporting and Analysis
Financial reporting and analysis are critical for understanding the financial health of a production operation. Production managers must be adept at interpreting financial statements, including income statements, balance sheets, and cash flow statements. These documents provide insights into profitability, liquidity, and overall financial stability.
Key aspects of financial reporting and analysis include:
- Understanding Key Metrics: Familiarize yourself with key performance indicators (KPIs) such as gross margin, net profit margin, and return on assets. These metrics help assess the efficiency and profitability of production operations.
- Variance Analysis: Conduct variance analysis to compare actual performance against budgeted figures. This process helps identify discrepancies and understand their causes, enabling better decision-making.
- Forecasting: Use historical data and market trends to forecast future financial performance. Accurate forecasting aids in strategic planning and resource allocation.
For example, if a production manager notices a consistent variance in labor costs, they can investigate the underlying causes—whether it’s due to overtime, inefficiencies, or staffing issues—and take corrective action.
Resource Allocation
Effective resource allocation is crucial for maximizing productivity and minimizing waste. Production managers must ensure that resources—such as labor, materials, and equipment—are allocated in a manner that supports operational goals.
To optimize resource allocation, production managers should:
- Assess Resource Needs: Evaluate the requirements of each production project and allocate resources accordingly. This assessment should consider factors such as project timelines, production capacity, and workforce availability.
- Prioritize Projects: Determine which projects are most critical to the organization’s success and allocate resources to those initiatives first.
- Utilize Technology: Implement resource management software to track resource usage and availability, enabling more informed decision-making.
For instance, if a production manager is overseeing multiple projects, they may need to prioritize a high-revenue project over others, reallocating resources to ensure timely completion and optimal output.
ROI and Cost-Benefit Analysis
Understanding the return on investment (ROI) and conducting cost-benefit analysis are vital for making informed financial decisions. ROI measures the profitability of an investment relative to its cost, while cost-benefit analysis evaluates the financial implications of different options.
To effectively assess ROI and conduct cost-benefit analysis, production managers should:
- Define Clear Objectives: Establish clear financial goals for each project or investment to measure success accurately.
- Calculate ROI: Use the formula ROI = (Net Profit / Cost of Investment) x 100 to determine the profitability of investments. A higher ROI indicates a more favorable investment.
- Conduct Cost-Benefit Analysis: List all potential costs and benefits associated with a project. This analysis helps determine whether the benefits outweigh the costs, guiding decision-making.
For example, if a production manager is considering investing in new machinery, they would calculate the expected increase in production efficiency and revenue against the cost of the machinery to determine if the investment is worthwhile.
Vendor and Supplier Management
Effective vendor and supplier management is essential for maintaining a smooth production process. Production managers must cultivate strong relationships with suppliers to ensure timely delivery of quality materials at competitive prices.
Key strategies for effective vendor and supplier management include:
- Establishing Clear Communication: Maintain open lines of communication with suppliers to discuss expectations, delivery schedules, and any potential issues that may arise.
- Evaluating Supplier Performance: Regularly assess supplier performance based on criteria such as quality, reliability, and cost-effectiveness. This evaluation helps identify areas for improvement and potential new suppliers.
- Negotiating Contracts: Negotiate favorable terms and conditions with suppliers to ensure the best possible pricing and service levels.
For instance, a production manager might implement a supplier scorecard system to evaluate and compare suppliers based on key performance indicators, ensuring that they are working with the best partners for their production needs.
Financial acumen is a multifaceted skill set that encompasses budgeting and cost control, financial reporting and analysis, resource allocation, ROI and cost-benefit analysis, and vendor and supplier management. By mastering these areas, production managers can significantly enhance their effectiveness, drive operational efficiency, and contribute to the overall success of their organizations.
Safety and Compliance
Exploring Regulatory Requirements
In the realm of production management, understanding and adhering to regulatory requirements is paramount. These regulations are designed to ensure the safety of employees, the quality of products, and the environmental impact of manufacturing processes. Production managers must familiarize themselves with local, national, and international regulations that pertain to their specific industry.
For instance, in the United States, the Occupational Safety and Health Administration (OSHA) sets forth guidelines that govern workplace safety. Compliance with OSHA standards not only protects workers but also shields the organization from potential legal repercussions. Similarly, industries such as food production must adhere to the Food and Drug Administration (FDA) regulations, which dictate safe handling and processing practices.
To effectively navigate these regulatory waters, production managers should:
- Stay updated on changes in legislation that may affect their operations.
- Engage with industry associations that provide resources and training on compliance.
- Consult legal experts when necessary to interpret complex regulations.
Implementing Safety Protocols
Once regulatory requirements are understood, the next step is to implement robust safety protocols. These protocols serve as the foundation for a safe working environment and should be tailored to the specific risks associated with the production process.
Effective safety protocols typically include:
- Risk Assessments: Conducting thorough risk assessments to identify potential hazards in the workplace. This involves evaluating machinery, materials, and processes to pinpoint areas that require attention.
- Standard Operating Procedures (SOPs): Developing clear SOPs that outline safe practices for each task. These documents should be easily accessible and regularly reviewed to ensure they remain relevant.
- Personal Protective Equipment (PPE): Ensuring that all employees are equipped with the necessary PPE, such as helmets, gloves, and goggles, to minimize exposure to hazards.
For example, in a manufacturing plant, a production manager might implement a protocol that requires all employees to wear safety goggles when operating machinery. This simple measure can significantly reduce the risk of eye injuries, demonstrating the importance of proactive safety measures.
Conducting Safety Audits
Regular safety audits are essential for maintaining compliance and ensuring that safety protocols are being followed. These audits involve a systematic examination of the workplace to identify potential hazards and assess the effectiveness of existing safety measures.
During a safety audit, production managers should:
- Inspect equipment and machinery for wear and tear.
- Review incident reports to identify patterns or recurring issues.
- Engage employees in discussions about safety concerns and suggestions for improvement.
For instance, if an audit reveals that several employees have reported near-miss incidents involving a particular machine, the production manager can take immediate action to address the issue, whether that means providing additional training, modifying the machine, or enhancing safety signage.
Training and Development in Safety Practices
Training is a critical component of any safety program. Production managers must ensure that all employees receive comprehensive training on safety practices relevant to their roles. This training should not be a one-time event but rather an ongoing process that evolves with the organization and its operations.
Key elements of effective safety training include:
- Orientation Programs: New employees should undergo a thorough orientation that covers safety protocols, emergency procedures, and the proper use of PPE.
- Regular Refresher Courses: Existing employees should participate in regular refresher courses to reinforce safety practices and introduce any new regulations or procedures.
- Hands-On Training: Practical, hands-on training sessions can help employees better understand how to apply safety protocols in real-world scenarios.
For example, a production manager might organize quarterly safety drills that simulate emergency situations, allowing employees to practice their responses in a controlled environment. This not only enhances their preparedness but also fosters a culture of safety within the organization.
Emergency Preparedness
Despite the best efforts to maintain a safe working environment, emergencies can still occur. Therefore, production managers must develop and implement comprehensive emergency preparedness plans. These plans should outline the steps to be taken in the event of various emergencies, such as fires, chemical spills, or natural disasters.
Key components of an effective emergency preparedness plan include:
- Emergency Response Team: Designating a team responsible for managing emergencies and ensuring that all employees know who to contact in case of an incident.
- Evacuation Procedures: Clearly defined evacuation routes and procedures should be established and communicated to all employees. Regular drills should be conducted to ensure everyone knows how to respond.
- Communication Plan: A robust communication plan is essential for disseminating information during an emergency. This includes notifying employees, emergency services, and stakeholders as necessary.
For instance, a production facility might implement a system that alerts employees via text message or an app in the event of an emergency, ensuring that everyone receives timely information and instructions.
Safety and compliance are critical aspects of a production manager’s role. By exploring regulatory requirements, implementing safety protocols, conducting audits, providing training, and preparing for emergencies, production managers can create a safer workplace that not only protects employees but also enhances overall productivity and efficiency.
Innovation and Continuous Improvement
In the fast-paced world of production management, the ability to innovate and continuously improve processes is paramount. Production managers are not just responsible for overseeing operations; they must also drive efficiency, enhance productivity, and foster a culture that embraces change. This section delves into the essential skills related to innovation and continuous improvement, providing insights into how production managers can effectively implement these strategies in their organizations.
Embracing Technological Advancements
Technology is a key driver of innovation in production management. As new tools and systems emerge, production managers must be adept at integrating these advancements into their operations. This requires a solid understanding of the latest technologies, such as automation, artificial intelligence (AI), and the Internet of Things (IoT).
For instance, consider a manufacturing plant that implements an AI-driven predictive maintenance system. This technology analyzes data from machinery to predict failures before they occur, allowing for timely maintenance and reducing downtime. A production manager who embraces such technology not only enhances operational efficiency but also saves costs associated with unexpected breakdowns.
Moreover, production managers should stay informed about emerging technologies through continuous learning and professional development. Attending industry conferences, participating in webinars, and engaging with technology vendors can provide valuable insights into how to leverage new tools effectively.
Process Improvement Methodologies
To foster a culture of continuous improvement, production managers should be well-versed in various process improvement methodologies. Techniques such as Lean Manufacturing, Six Sigma, and Kaizen are widely recognized for their effectiveness in enhancing operational efficiency.
Lean Manufacturing focuses on eliminating waste and optimizing processes. For example, a production manager might implement Lean principles by streamlining workflows, reducing excess inventory, and improving layout designs to minimize movement and transportation time.
Six Sigma emphasizes reducing variability and defects in processes. A production manager can utilize Six Sigma tools, such as DMAIC (Define, Measure, Analyze, Improve, Control), to identify root causes of inefficiencies and implement data-driven solutions. For instance, if a production line experiences frequent delays, a Six Sigma analysis might reveal that a specific machine is underperforming, prompting targeted improvements.
Kaizen, which means “continuous improvement” in Japanese, encourages small, incremental changes that lead to significant enhancements over time. A production manager can foster a Kaizen culture by involving employees at all levels in identifying areas for improvement and implementing their suggestions. This not only boosts morale but also empowers the workforce to take ownership of their processes.
Encouraging a Culture of Innovation
Creating a culture of innovation within a production environment is essential for long-term success. Production managers play a crucial role in fostering this culture by encouraging creativity, collaboration, and open communication.
One effective strategy is to establish cross-functional teams that bring together employees from different departments. These teams can brainstorm innovative solutions to common challenges, share diverse perspectives, and drive collaborative problem-solving. For example, a production manager might form a team comprising members from engineering, quality assurance, and operations to develop a new product line, ensuring that all aspects of production are considered from the outset.
Additionally, production managers should recognize and reward innovative ideas and initiatives. Implementing an employee recognition program that highlights contributions to innovation can motivate staff to think creatively and propose new solutions. For instance, a monthly award for the best improvement suggestion can inspire employees to actively participate in the innovation process.
Benchmarking and Best Practices
Benchmarking is a powerful tool for production managers seeking to drive continuous improvement. By comparing their processes and performance metrics against industry standards or competitors, production managers can identify gaps and areas for enhancement.
For example, a production manager might analyze key performance indicators (KPIs) such as production cycle time, defect rates, and overall equipment effectiveness (OEE) against those of leading companies in the same sector. This analysis can reveal best practices that can be adopted to improve efficiency. If a competitor has a significantly lower defect rate, the production manager can investigate their quality control processes and implement similar strategies.
Moreover, attending industry forums and networking with peers can provide valuable insights into best practices. Production managers can learn from the successes and challenges faced by others, adapting these lessons to their own operations.
Feedback and Iteration
Continuous improvement is an iterative process that relies heavily on feedback. Production managers must establish mechanisms for gathering input from employees, customers, and stakeholders to inform their improvement efforts.
One effective approach is to conduct regular feedback sessions with frontline employees who are directly involved in production processes. These sessions can uncover valuable insights into operational challenges and potential solutions. For instance, a production manager might hold weekly meetings where employees can voice concerns, suggest improvements, and discuss obstacles they face on the production floor.
Additionally, customer feedback is crucial for driving innovation. Production managers should actively seek input from customers regarding product quality, features, and performance. This feedback can guide product development and enhancements, ensuring that the production process aligns with customer expectations.
Finally, production managers should embrace a mindset of experimentation. Implementing pilot projects or trial runs for new processes or technologies allows for real-world testing and evaluation. By analyzing the results and gathering feedback, production managers can make informed decisions about scaling successful initiatives across the organization.
The skills related to innovation and continuous improvement are vital for production managers. By embracing technological advancements, applying process improvement methodologies, fostering a culture of innovation, benchmarking against best practices, and actively seeking feedback, production managers can drive significant enhancements in their operations. This proactive approach not only improves efficiency and productivity but also positions organizations for long-term success in an ever-evolving industry landscape.
Interpersonal Skills
Interpersonal skills are crucial for production managers, as they play a significant role in fostering a productive work environment, enhancing team dynamics, and ensuring smooth operations. These skills encompass a range of abilities that facilitate effective communication, collaboration, and relationship-building among team members, stakeholders, and clients. We will explore the key components of interpersonal skills, including building strong relationships, emotional intelligence, networking and professional development, team building activities, and mentoring and coaching.
Building Strong Relationships
At the heart of effective production management lies the ability to build strong relationships. Production managers interact with various stakeholders, including team members, suppliers, clients, and upper management. Establishing trust and rapport with these individuals is essential for fostering a collaborative work environment.
To build strong relationships, production managers should:
- Communicate Effectively: Clear and open communication is vital. Production managers should practice active listening, ensuring they understand the needs and concerns of their team members. This involves not only hearing what is said but also interpreting non-verbal cues and responding appropriately.
- Show Appreciation: Recognizing and appreciating the contributions of team members can significantly enhance relationships. Simple gestures, such as thanking someone for their hard work or acknowledging their achievements in team meetings, can go a long way in building morale and loyalty.
- Be Approachable: Creating an environment where team members feel comfortable approaching the production manager with their ideas, concerns, or feedback is crucial. This can be achieved by maintaining an open-door policy and being receptive to input from all levels of the team.
For example, a production manager who regularly holds one-on-one meetings with team members can foster a sense of belonging and ensure that everyone feels valued. This practice not only strengthens relationships but also helps identify potential issues before they escalate.
Emotional Intelligence
Emotional intelligence (EI) is the ability to recognize, understand, and manage one’s own emotions while also being aware of and influencing the emotions of others. For production managers, high emotional intelligence is essential for navigating the complexities of team dynamics and workplace challenges.
Key components of emotional intelligence include:
- Self-Awareness: Understanding one’s own emotions and how they affect behavior is the first step in developing emotional intelligence. Production managers should regularly reflect on their emotional responses and consider how these may impact their interactions with others.
- Self-Regulation: The ability to control one’s emotions and reactions is crucial in high-pressure environments. Production managers should practice techniques such as mindfulness and stress management to maintain composure during challenging situations.
- Empathy: Being able to empathize with team members allows production managers to understand their perspectives and feelings. This understanding can lead to more effective communication and conflict resolution.
- Social Skills: Strong social skills enable production managers to build networks, influence others, and manage relationships effectively. This includes skills such as conflict resolution, negotiation, and teamwork.
For instance, a production manager who notices a team member struggling with a task can use their emotional intelligence to approach the situation with empathy, offering support and guidance rather than criticism. This not only helps the individual but also strengthens the overall team dynamic.
Networking and Professional Development
Networking is an essential aspect of professional development for production managers. Building a robust professional network can provide valuable resources, insights, and opportunities for collaboration. Engaging with peers in the industry can lead to the exchange of best practices, innovative ideas, and potential partnerships.
To effectively network, production managers should:
- Attend Industry Events: Participating in conferences, trade shows, and workshops allows production managers to meet industry leaders, learn about emerging trends, and share experiences with peers.
- Join Professional Organizations: Becoming a member of relevant professional organizations can provide access to resources, training, and networking opportunities. Organizations often host events, webinars, and forums that facilitate connections among professionals in the field.
- Utilize Social Media: Platforms like LinkedIn offer production managers the opportunity to connect with other professionals, share insights, and stay updated on industry news. Engaging in discussions and sharing content can enhance visibility and credibility within the industry.
For example, a production manager who actively participates in industry forums may discover new technologies or methodologies that can improve their production processes. Additionally, these connections can lead to mentorship opportunities or collaborations on projects.
Team Building Activities
Team building activities are essential for enhancing collaboration, communication, and trust among team members. Production managers should prioritize these activities to create a cohesive team that works well together, especially in high-pressure environments where teamwork is critical for success.
Effective team building activities can include:
- Workshops and Training Sessions: Organizing workshops focused on skill development or problem-solving can help team members learn from each other and strengthen their working relationships.
- Team Retreats: Off-site retreats provide an opportunity for team members to bond outside of the usual work environment. These retreats can include team-building exercises, brainstorming sessions, and social activities that foster camaraderie.
- Regular Team Meetings: Holding regular team meetings that encourage open dialogue and collaboration can help build a sense of unity. These meetings should focus on not only project updates but also team dynamics and individual contributions.
For instance, a production manager who organizes a team-building retreat that includes both fun activities and strategic planning sessions can help team members connect on a personal level while also aligning their goals and objectives.
Mentoring and Coaching
Mentoring and coaching are vital components of interpersonal skills for production managers. By investing time in developing their team members, production managers can enhance individual performance and contribute to the overall success of the production team.
To effectively mentor and coach team members, production managers should:
- Set Clear Goals: Establishing clear, achievable goals for team members helps provide direction and motivation. Production managers should work with individuals to identify their strengths and areas for improvement, setting specific objectives for development.
- Provide Constructive Feedback: Regular feedback is essential for growth. Production managers should offer constructive criticism that focuses on behaviors and outcomes rather than personal attributes. This approach encourages improvement while maintaining a positive relationship.
- Encourage Continuous Learning: Supporting team members in pursuing further education, certifications, or training opportunities demonstrates a commitment to their professional growth. Production managers can facilitate this by providing resources or time for learning.
For example, a production manager who takes the time to mentor a junior team member by providing guidance on project management techniques can help that individual develop valuable skills while also fostering a sense of loyalty and commitment to the team.
In summary, interpersonal skills are a cornerstone of effective production management. By focusing on building strong relationships, developing emotional intelligence, engaging in networking and professional development, facilitating team building activities, and committing to mentoring and coaching, production managers can create a positive and productive work environment that drives success.
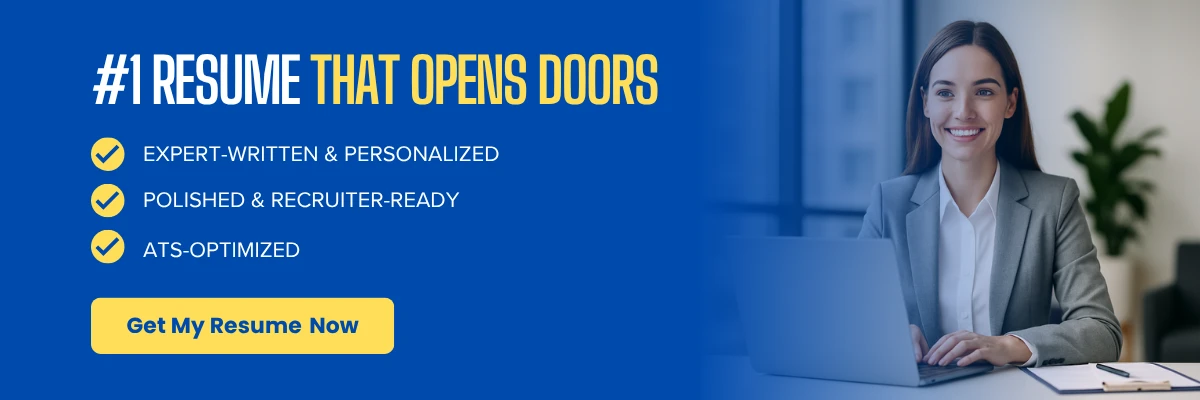
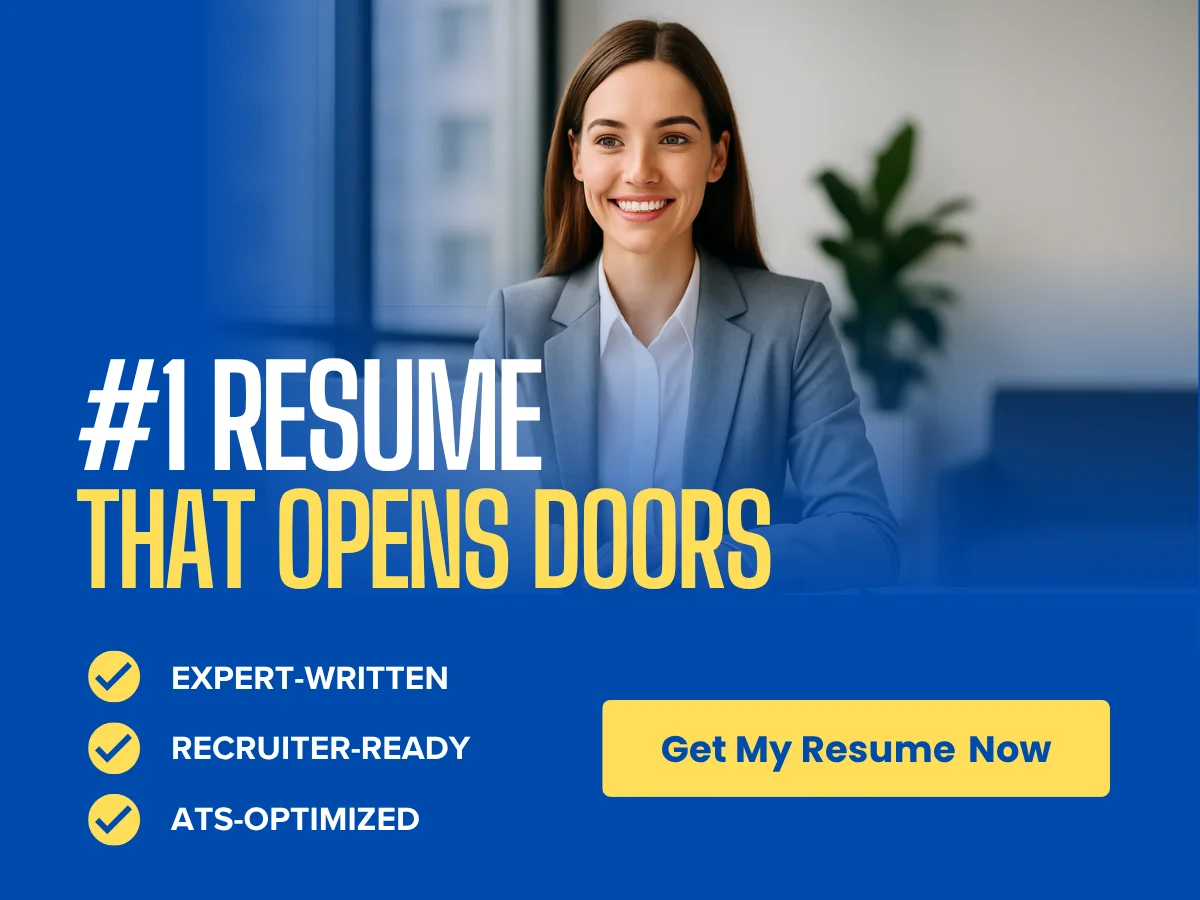